BALANCE SPRING / HAIRSPRING
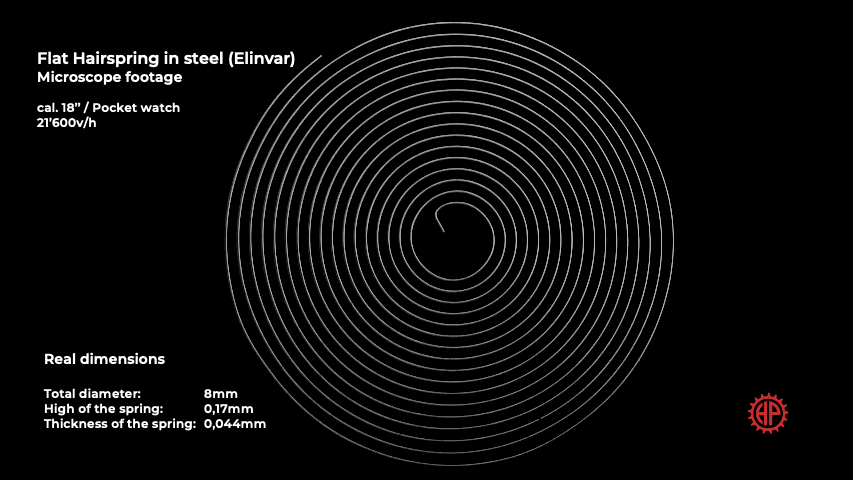
The hairspring serves the same purpose on a watch’s balance wheel as gravity does on a clock’s pendulum. Their role is to consistently bring the oscillator (balance wheel or pendulum) back to the midpoint of its amplitude – to the rest point (named so because it’s the position the oscillator occupies when it no longer receives energy and stops). The central end of the hairspring is affixed to the balance staff via a collet (a movable part). The peripheral end of the hairspring is attached to the cock via a stud (fixed point).
When the lever transmits its impulse to the balance wheel, it initiates its free oscillation. The hairspring expands, slowing the balance wheel until it stops, then brings it back to the rest point. The balance wheel then receives an impulse that initiates an opposite oscillation. The hairspring contracts, bringing the balance wheel back to the rest point.
The responsibility for precision lies with the hairspring. Whether the energy of the impulses transmitted to the balance wheel is maximal or minimal regardless of the angle covered by the balance wheel (amplitude), each oscillation must have exactly the same duration (period). The active length of the hairspring determines the accuracy of the watch’s regulation. If the hairspring is too short, the watch gains time; if it is too long, the watch loses time. Watches equipped with an index allow for the adjustment of the active length of the hairspring, determined in this case by the position of the two index pins. Since the hairspring does not develop perfectly concentrically to the balance staff axis, it creates balance defects in vertical positions. To change this, some watchmakers decided to modify the outer coil of the hairspring. By raising it, bringing it back above the horizontal plane of the hairspring, and attaching it in this position to the cock, the concentricity of the hairspring is significantly improved when in operation (Breguet overcoil, Philips terminal curve). Cylindrical (helical), spherical hairsprings with double terminal curves allow for a nearly concentric development of the hairspring. Their complex fabrication and the space they require limit their use in wristwatches to a few exceptional timepieces.
Due to the numerous factors influencing its proper functioning, precision, and accuracy required at every step of its production (from alloy casting to final regulation), the hairspring is rightly considered the most important, sensitive, and challenging component to produce.
If the traditional production of steel hairsprings (from Elinvar) persists, it is, at most, only from a dozen manufacturers. The advent of silicon in the early 2000s led to its market share exploding in hairspring production.
In 1675, Christian Huygens, who had discovered the theory of the pendulum twenty years earlier, presumably assisted by the preliminary work of the abbot Jean de Hautefeuille in France and Dr. Robert Hooke in England to create the first watch regulated by a hairspring. This was the inception of the era of portable clocks (travel clocks), navigation instruments (marine chronometers), and pocket watches, which led to the foundation of mechanical horology’s technical principles. These principles have been continuously improved since by knowledge and technological advancements, however, remain unchanged in their base to this day.
Watchmakers embraced Huygens’ principle and quickly realized the significant influence of thermal variations and balance (concentric development of the hairspring). In 1766, John Harrison devised a thermal compensation system. A bimetallic strip controls the movements of the regulator to correct the active length of the hairspring as it expands or contracts. Renowned watchmakers such as Ferdinand Berthoud, Pierre Le Roy, or Abraham-Louis Breguet refined Harrison’s work or devised their own thermal compensation solutions (bimetallic balance wheel, etc.).
In 1782, John Arnold patented a cylindrical hairspring. It developed concentrically to the balance staff axis, unlike Huygens’ flat hairspring. This type of hairspring allows for exceptional chronometry, especially when paired with a detent escapement. Chronometry, navigation, and exploration benefited from this true revolution. The cylindrical hairspring requires many more manufacturing steps and expertise than a flat hairspring and demands a space that can significantly affect the thickness of a movement. Therefore, its use in wearable watches is limited to a few exceptional timepieces.
It wasn’t until 1919 that Charles-Edouard Guillaume, who had invented Invar twenty-five years earlier, developed Elinvar (elastic and invariable). This nickel-iron-chromium alloy revolutionized hairsprings with its low expansion coefficient, ideal elasticity, and low sensitivity to magnetic fields. Along with his work on Invar, Guillaume won the Nobel Prize in Physics in 1920, and Elinvar is still the alloy used in the traditional production of hairsprings.
Since 2000, the application of photolithographic silicon production technologies has revolutionized the world of hairsprings. This method of production requires a great deal of expensive technology, but the process is simple to master. It enables high-quality, high-volume production. Finally, silicon has excellent elasticity, is non-magnetic and remarkably resistant to wear and corrosion. Since its inception, this production method has been booming.
This method still employs the Elinvar alloy, invented by Charles-Edouard Guillaume, and is used primarily in watchmaking in minimal quantities. Only a handful of producers offer it at a considerable cost. Alloy producers (foundries) deliver Elinvar in a wire of approximately 0.8-1mm in diameter. The initial steps in crafting a hairspring involve drawing this wire to reduce its diameter. The wire is pulled through successive dies, gradually decreasing its diameter while increasing its length. No material is eliminated (machined) during these operations. Once the calculated diameter of the wire is reached, various rolling steps follow. The principle is similar to drawing, but this time, the wire is pulled between rollers until it achieves the desired rectangular section. Once the section dimensions are attained, the blades can be cut to their nearly final length. The spring’s shape is then formed by winding multiple blades onto drums (collets), which undergo various heat treatments extremely sensitive to perform. The springs solidify in their final form and acquire their elastic properties. The spring’s length is then refined (inner and outer cuts), the outer curve is formed, the collet is fixed inside, and the stud is attached outside. Its elasticity module is then measured with a highly precise instrument that also measures the balance wheel’s inertia. This step allows for an ideal balance wheel-hairspring pairing for optimal chronometry. Finally, the hairspring can be fitted onto its balance wheel’s staff, and the numerous manual steps of centring, flattening, balancing, and regulation can be executed. These stages can only be carried out by hand and require exceptional dexterity.
Less than 10 names mastered this production method among brands or subcontractors. Many watchmakers and Maisons are thus compelled to source from them.
Emerging in watchmaking since the year 2000, silicon has truly revolutionized the production of many components, especially the hairspring. While the production technology is complex, the process requires much less expertise and often involves only one automated step. This method is used for the fabrication of integrated circuits. The principle involves cutting a silicon wafer to a given thickness (generally that of the finished component) using a photolithographic process. This method can achieve the most complex profiles with precision reaching the micron. Depending on the size of the components to be produced, several hundred pieces can be made simultaneously on the same substrate wafer. The most complex profiles can be obtained without the drawback of the radii of a milling tool or even the wire of an EDM machine. This process exerts no mechanical stress, allowing for the creation of very thin components (springs, etc.) or perforating them to reduce weight. Silicon is harder than steel, has an excellent elasticity module, and is non-magnetic. Advances in this technology and its success make it increasingly attractive in terms of production costs and tend to become widespread for the production of many components (especially for the escapement and regulating organ).