SLIDING PINION
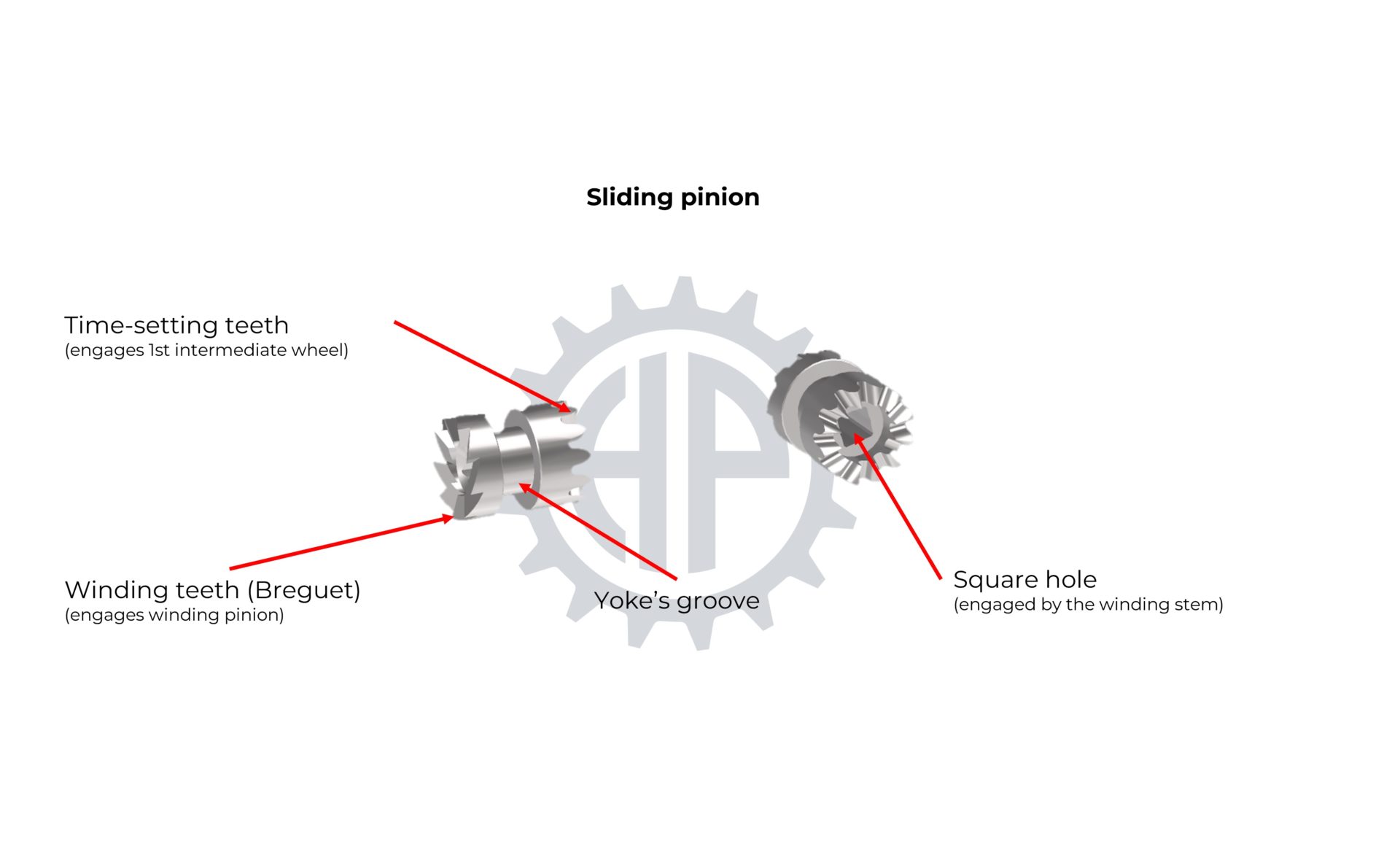
The sliding pinion is a steel cylinder with the unique feature of teeth at each end. It is commonly part of both the winding and time-setting mechanisms. Its axis is pierced with a square hole that allows it to fit onto the winding stem. This square fitting enables the winding stem to drive the sliding pinion when the crown is turned. The length of the square on the winding stem exceeds the length of the sliding pinion, allowing the latter to slide linearly along the axis of the stem. A groove turned in the centre of the sliding pinion accommodates the yoke’s lever. When the crown (and thus the winding stem) is pushed, the yoke positions the sliding pinion against the winding pinion, with which it engages through a unidirectional Breguet-type teeth system. When the crown is pulled (and thus the winding stem), the setting lever activates the yoke, causing the sliding pinion’s second set of teeth to engage with the time-setting mechanism.
The invention of the sliding pinion can be attributed to Antoine Le Coultre when he invented the setting lever mechanism in 1847. This innovation allowed the watch to be wound and set without a key, using the same control (the crown). In almost two centuries, the mechanism has not undergone significant evolution and remains the most used mechanism today.
A lathe is sufficient to fully manufacture a sliding pinion. The turning operations are minimal (clearing the two faces to release the teeth and the groove of the yoke). It is also necessary to drill the pinion. If a small milling cutter allows, a square hole can be milled directly on the lathe. Another solution is to drill a cylindrical hole and then manually file the square. Before removing the pinion from the lathe, its two sets of teeth can be milled directly, and finishing can be applied.
As with most small-diameter circular components, the automatic lathe is the ideal machine for producing sliding pinions in any quantity. This method allows for the quick completion of all operations (turning, cutting, milling the square) in a single cycle. Regardless of the desired quality, machining a sliding pinion using this method takes only a few minutes.