MICROMETRIC ADJUSTMENT SCREW
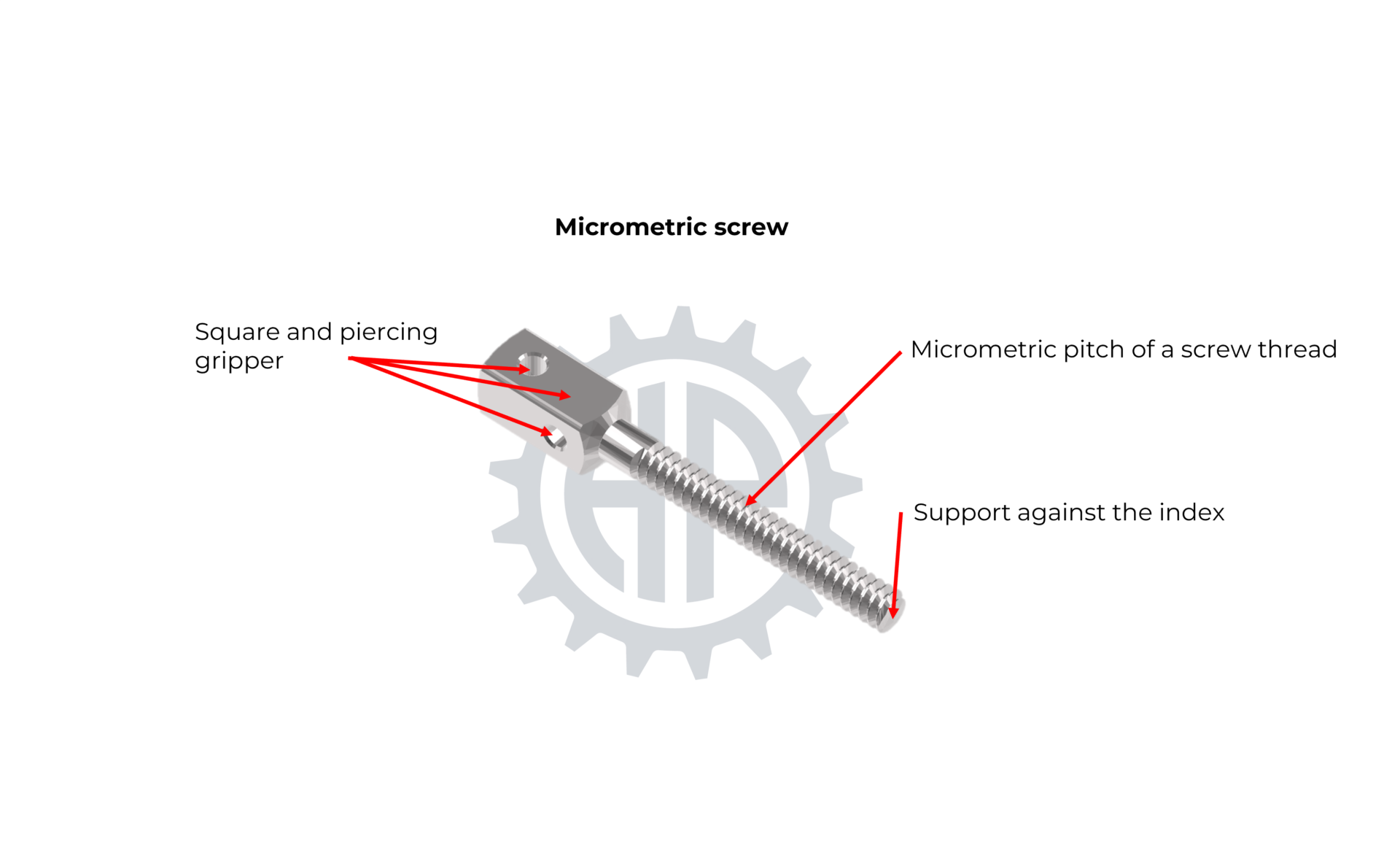
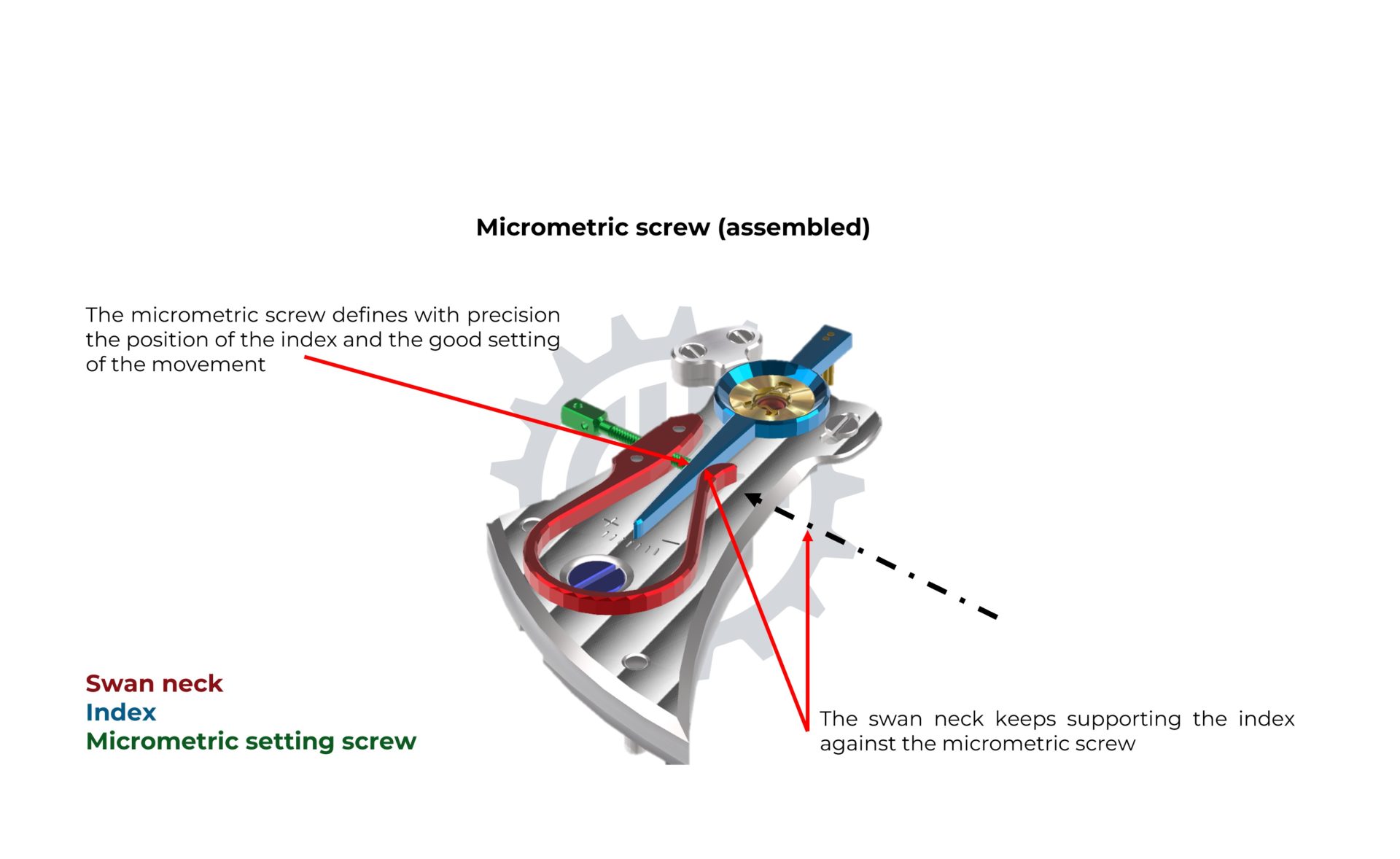
The micrometric adjustment screw is an integral yet optional component of the swan neck.
It allows for precise adjustment of the watch’s rate (advance-retard) and its maintenance. The micrometric adjustment screw passes through the heel of the swan neck into which it is screwed. The swan neck presses the index support against the end of the micrometric adjustment screw. The thread pitch of the adjustment screw is very tight, allowing for a very fine adjustment of the position of the index. By keeping the index against the micrometric adjustment screw, the swan neck prevents any unintended misregulation, especially during shocks.
Dating the appearance of the micrometric adjustment screw and the swan neck is challenging, and attributing paternity is even more so. The first observed systems date back to the 18th century. However, the use of such systems experienced a boom between the late 19th and early 20th centuries.
Made of steel, the micrometric adjustment screw is a relatively easy component to manufacture regardless of the method. The artisan begins by performing all the turning operations, which constitute the bulk of the work. The same lathe can be used to thread the screw. The head of the screw is then decorated, and it may undergo heat treatments (quenching and tempering). The heat treatments of the micrometric adjustment screw are relatively challenging due to its significant length and small diameter. Thus, the heat treatment may not be uniform, and deformations of the screw are unfortunately always possible during these stages. A brief polishing and softening stage will rewhiten the screw, making it ready for assembly.
Automatic lathe is the most suitable machine for producing micrometric adjustment screws regardless of the quantity. All operations (turning, threading, and milling of the square gripper, if applicable) can be performed in a single cycle. Depending on the chosen steel alloy, the micrometric adjustment screw may not require additional heat treatments. Finally, depending on the level of finishes chosen, the terminations, especially polishing, can be done by hand, or more industrially in bulk (e.g., in a polishing drum).