SWAN NECK
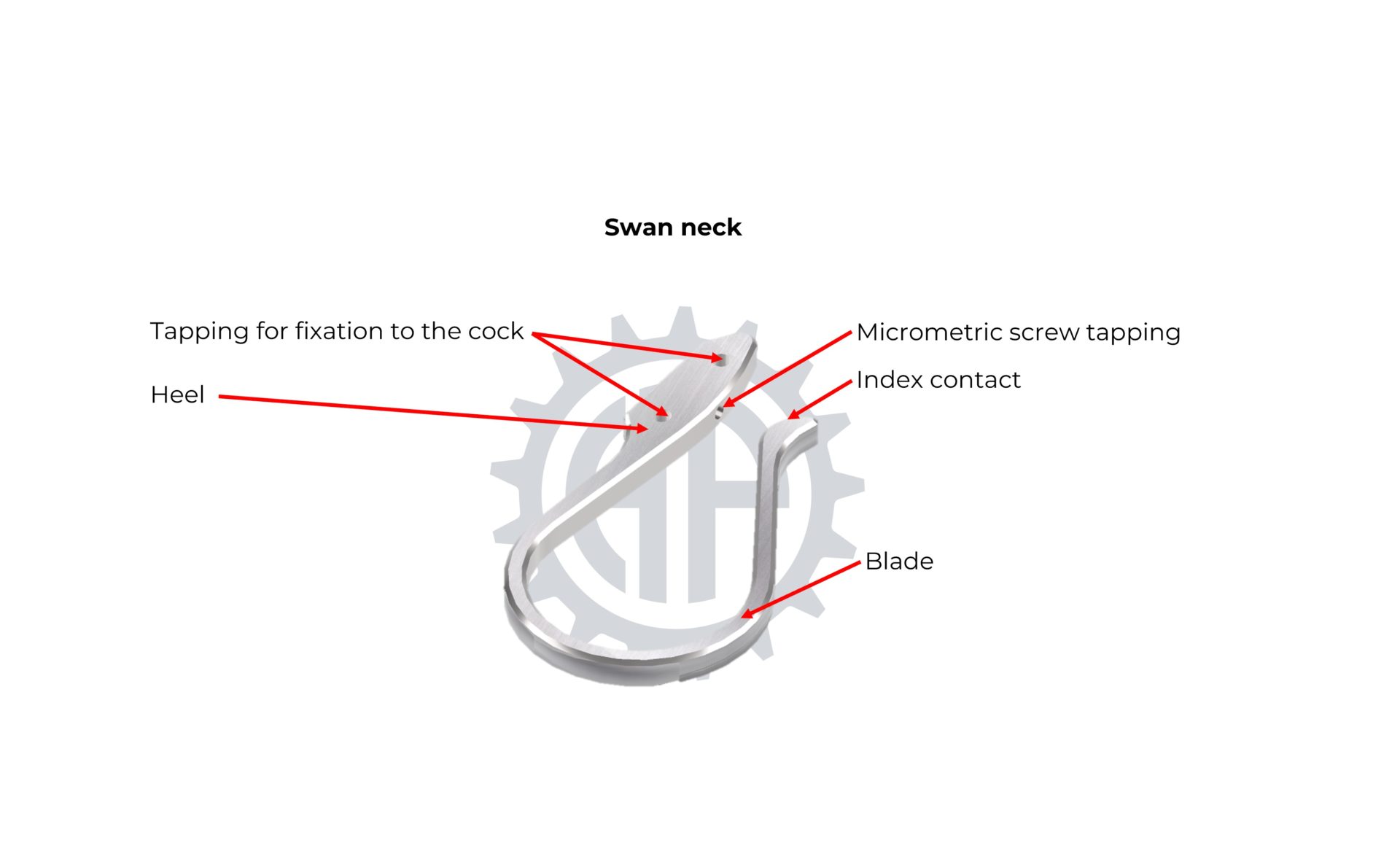
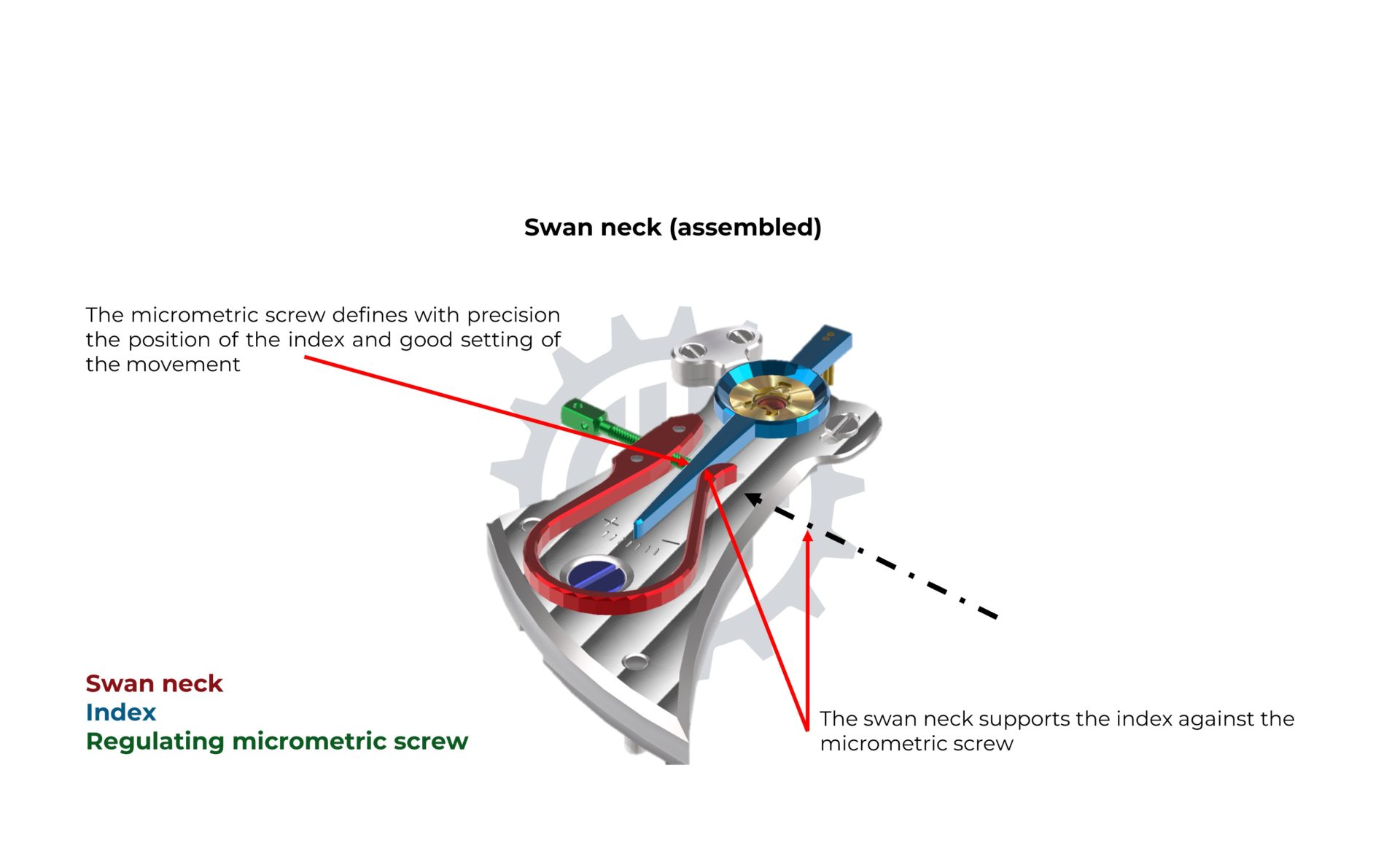
A swan neck is an elegant steel spring exclusively reserved for watches equipped with a flat hairspring and a certain level of craftsmanship. Its name is derived from its distinctive shape. The swan neck screws onto the upper surface of the balance bridge, and “embraces” the tail of the index. Technically, the swan neck serves a dual purpose. It presses the index against the buffet formed by the micrometric screw associated with the swan neck, ensuring that the adjustment established by the watchmaker remains the same and is not likely to be altered by an impact or a shock. The combination of the swan neck and its micrometric screw allows for a much finer adjustment than a traditional system lacking the swan neck-micrometric screw tandem.
It is challenging to attribute the invention of the swan neck and the date of its creation. It is posterior to the invention of the balance wheel–hairspring by Christian Huygens in 1675. It seems that the swan neck emerged as chronometry underwent significant developments during the 19th century. Such mechanisms persist in high-end traditional watchmaking today; however, similar mechanisms have been developed since then (e.g., a double-armed index adjusted and constrained in position by an eccentric stud). Such systems achieve the same level of technical and functional results for a lower production cost. They simply do not offer the same aesthetic qualities as a finely beveled swan neck.
The watchmaker begins the artisanal production of a swan neck by tracing its profile with a tracing tool on the surface of a steel plate slightly thicker than the finished component. The various holes (for screws and feet) are then centered and drilled. The spring’s contours are delicately cut using a piercing saw. The spring’s sides are then filed to bring them to their final thickness while adhering to their absolute form. The spring’s heel and blade are then beveled and polished using standard tools (files, buff sticks, polishing). These operations are particularly delicate due to the length, fineness, and shape of the swan neck’s blade. According to the rules of the craft, the artisan then stretches the lines of the spring’s sides (satin-finish) and the small remaining flat surface on the top.
The heat treatments and subsequent whitening operations are also particularly delicate due to the length, shape, and fineness of the spring. The optional nature of the swan neck, its artisanal dimension, and thus the time and cost required for its production make it a component reserved for watches of a certain level of craftsmanship (in quality and price).
To enhance the cost-effectiveness of manufacturing a single piece or a small series of components, the electrical discharge process proves particularly advantageous. Implementation costs and machine passage time remain relatively low and suitable for small production volumes. Moreover, this technology allows for cutting complex and fine profiles, such as the swan neck, without exerting any mechanical stress on the component during production. Compared to artisanal methods, the electrical discharge process offers a considerable time-saving with positive impacts on the final finishing. The end of the manufacturing and decoration process resembles the artisanal method. Generally, the manufacturing cost of a swan neck is so high that it is reserved for high-range watches. Therefore, the finishing applied to it mostly falls under the realm of high-end artisanal watchmaking.
For mass production, investing in a stamping tool is justified to manufacture swan necks at an optimal cost. The enlarged contour of the profile is punched directly into a strip of steel slightly thicker than the finished component using a stamping press. However, manual steps are still unavoidable. Subsequently, the feet that will facilitate its positioning on the balance cock need to be added. The spring must then be brought to its final dimensions (profile and thickness) while providing the desired finishing and decorations (satin-finish, angling, etc.).