CROWN WHEEL
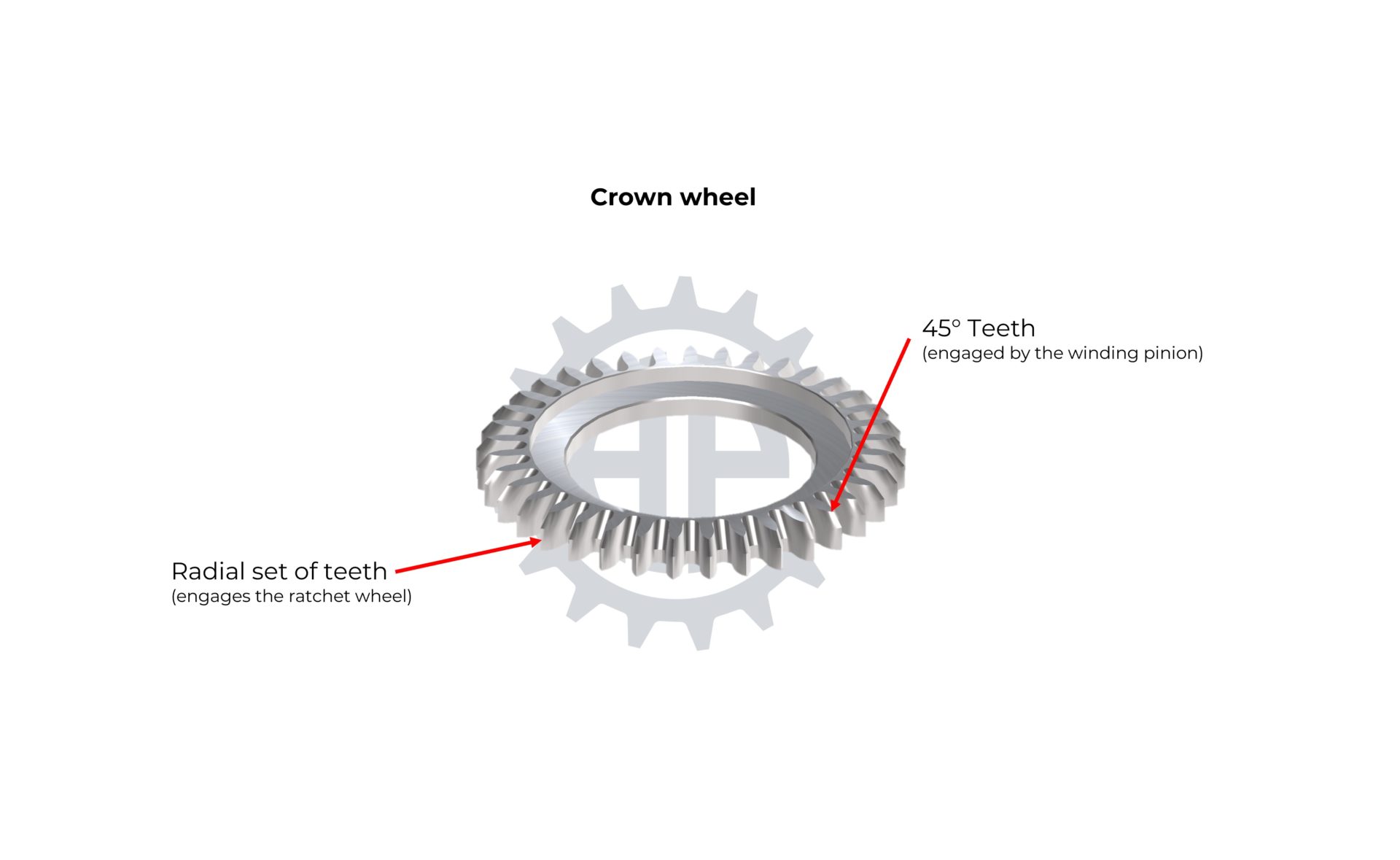
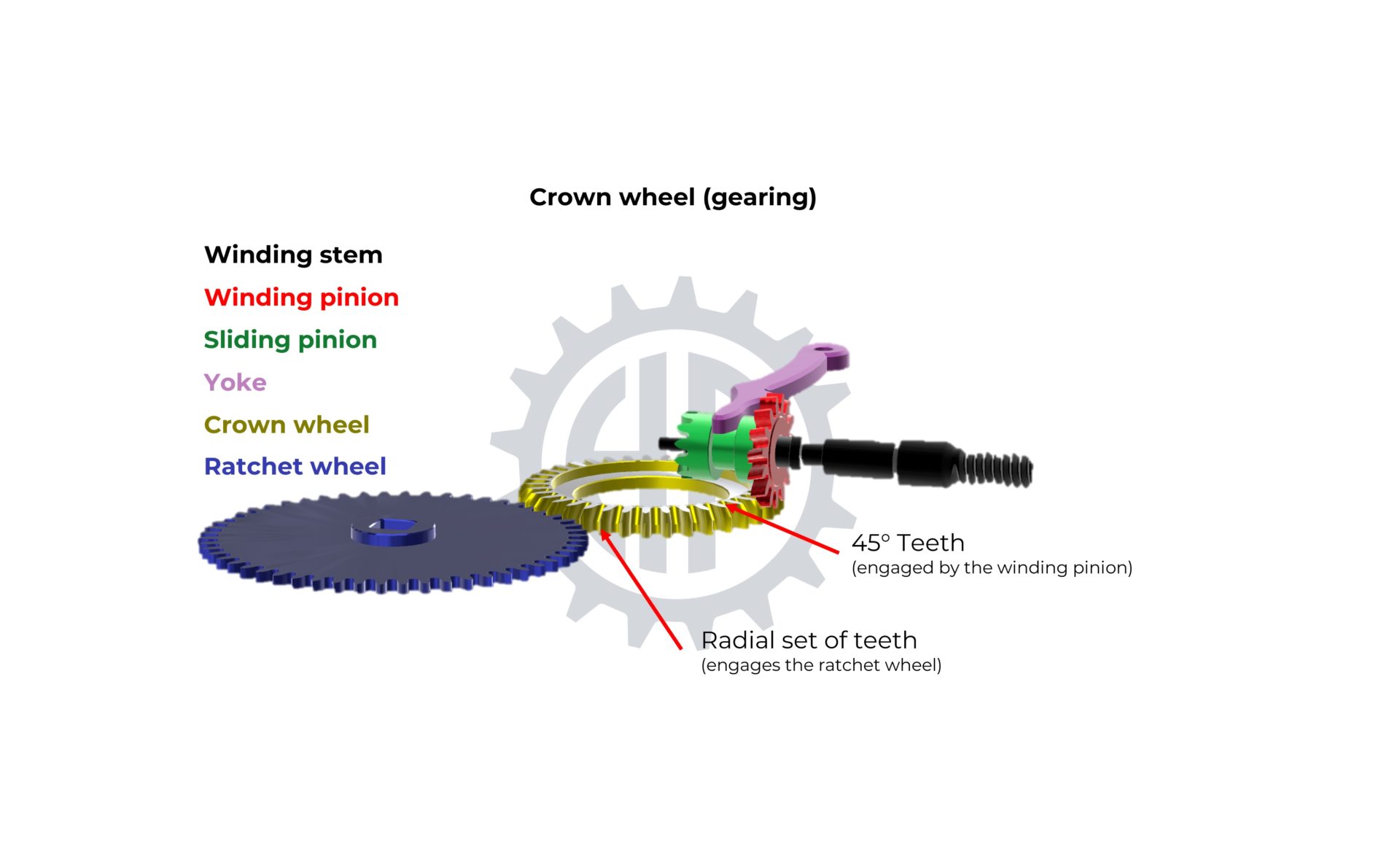
The crown wheel is the penultimate moving component in the winding mechanism. Its role is to transmit the energy from the winding mechanism (winding stem, sliding pinion, and winding pinion) to the ratchet wheel, which will arm the barrel spring. The gear train of the winding mechanism is a gear reducer, with each rotating element moving more slowly than the previous one. This design increases the number of crown (and winding stem) turns required to fully wind the barrel spring but requires much less torque (force) to achieve this. The calculation of the reduction of the winding train is therefore a subtle compromise (the watch winding process should neither be too long nor too difficult).
In addition to transmitting energy to the ratchet wheel, the crown wheel modifies the gear train’s plane. Indeed, the axis of the winding pinion positions it on a vertical plane, while the crown wheel and the ratchet wheel operate on a horizontal plane. Hence, a double set of teeth is cut on the periphery of the crown wheel: one on the vertical plane (underneath the crown wheel) engages with the winding pinion, and the second, on the horizontal plane (on the crown wheel’s periphery), engages with the ratchet. It is this double “crown” tooth profile that likely gives it its name. Due to the torques present in this gear train, all its components are made of steel. This includes the crown wheel, which pivots on a core with the largest possible diameter. The rotation axis of the crown wheel thus better absorbs the forces present and guarantees a sustainably low level of friction.
The appearance and the invention of the crown wheel are linked to Adrien Philippe’s discovery of the keyless winding mechanism in 1842. Before him, other watchmakers had conceived such mechanisms but failed to miniaturise them sufficiently to be acceptable for a pocket watch of that era. The success of such a mechanism, therefore, resided more in its miniaturisation than in its mechanical principle. Adrien Philippe’s solution, still in use today, involves distributing the mechanism on a vertical axis (sliding pinion and winding pinion) and a horizontal axis (crown wheel, ratchet wheel). The crown wheel and its double tooth profile thus constitute, in a way, the keystone of the design of winding mechanisms since their inception.
Exclusively made of steel, the crown wheel is relatively easy to manufacture. According to traditional methods, a lathe equipped with a dividing head allows for all its manufacturing stages. Turning operations come first. The crown wheel’s double tooth profile and its pivoting on its core make these numerous and require a high level of precision. It is preferable to cut both tooth profiles successively on the same lathe without interruption to ensure the concentricity of the assembly (turning and teeth). These operations are carried out with specific milling cutters and a dividing head mounted on the lathe. Once cut from its bar, the crown wheel can be made thicker to adjust its pivoting and height clearance. Heat treatments and decoration (usually sunbursting) will complete the manufacturing steps according to traditional methods.
As with most circular components of small diameter, the automatic lathe is the best (and only) way to produce crown wheels using the industrial method. All machining operations (turning, milling, cutting) can be performed in a fast cycle without particular difficulty. As always on an industrial scale, finishing and decoration will be done by hand or industrially, depending on the required level of finishes and the watch’s range.