LE SPIRAL
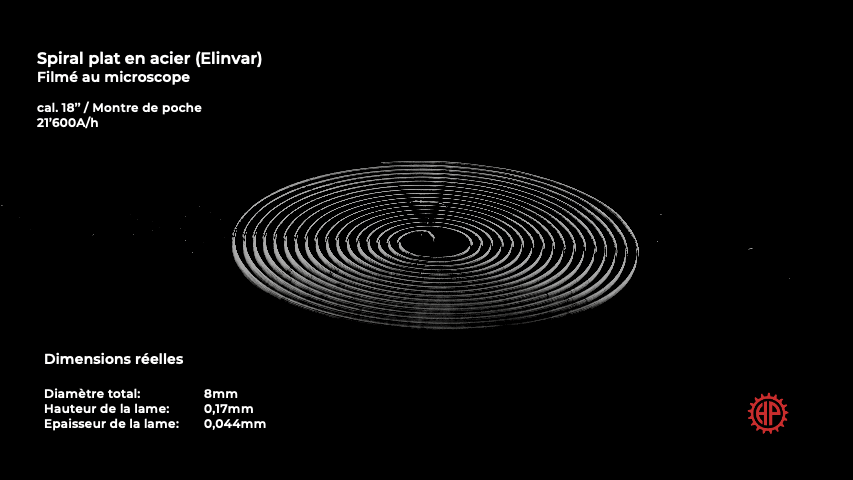
Le spiral a la même fonction sur le balancier d’une montre, que la gravité sur le pendule d’une horloge. Leur rôle est de ramener constamment l’oscillateur (balancier ou pendule) au point médiant de son amplitude : Le point de repos (nommé ainsi car c’est la position qu’occupe l’oscillateur lorsqu’il ne reçoit plus d’énergie et s’arrête). L’extrémité centrale du spiral se fixe à l’axe de balancier par l’intermédiaire d’une virole (partie mobile). L’extrémité périphérique du spiral se fixe au coq par l’intermédiaire d’un piton (point fixe).
Lorsque l’ancre transmet son impulsion au balancier celui-ci commence son alternance libre. Le spiral se dilate, freine le balancier jusqu’à l’arrêter et le rappelle au point de repos. Le balancier reçoit alors une impulsion qui lance une alternance opposée. Le spiral, se contracte alors et ramène également le balancier à son point de repos.
C’est au spiral qu’incombe la responsabilité de la précision. Que l’énergie des impulsions transmises au balancier soit maximale ou minimale et quelque soit l’angle parcouru par le balancier (amplitude), Chaque alternance doit avoir exactement la même durée (période). La longueur active du spiral détermine la précision du réglage de la montre. Si le spiral est trop court, la montre avance, s’il est trop long, la montre retarde. Les montres étant équipées d’une raquette permettent de modifier la longueur active du spiral, déterminée dans ce cas par la position des deux goupilles de raquette. Le spiral ne se développant pas de manière parfaitement concentrique à l’axe du balancier, il créé, dans les positions verticales, des défauts d’équilibre préjudiciables. Forts de ce constat, certains horlogers eurent l’idée de modifier la spire extérieure du spiral. En relevant celle-ci, en la faisant revenir au-dessus du plan horizontal du spiral et en l’attachant dans cette position au coq on améliore considérablement la concentricité du spiral lorsqu’il travaille (courbe terminale Breguet, courbe terminale Philips). Des spiraux cylindriques (hélicoïdaux), sphériques à double courbes terminales permettent un déveleppement quasi concentrique du spiral. Leur fabrication complexe et l’encombrement qu’ils exigent, limitent leurs applications en montre-bracelets à quelques montres d’exception.
Par les nombreux facteurs influant sur sa bonne marche, par la précision, l’exactitude que requièrent toutes les étapes de sa fabrication (de la coulée de l’alliage au réglage final), le spiral est justement considéré comme le composant le plus important, sensible et difficile à produire. Le spiral est certainement le composant qui demande le plus de compétences et le plus d’expertise dans sa fabrication.
Si la fabrication traditionnelle de spiraux en acier (Elinvar) perdure, elle n’est issue, tout au plus, que d’une dizaine de maisons.
En 1675, Christian Huygens, qui a découvert la théorie du pendule (isochronisme) vingt ans auparavant, probablement aidé par les travaux préliminaires de l’Abbé de Hautefeuille en France et du Docteur Robert Hooke en Angleterre, fait fabriquer la première montre régulée par un balancier-spiral. Les horloges portables (horloges de voyages), de navigation (chronomètres de marine) et les montres pouvaient dès lors exister et donner à l’horlogerie mécanique les fondements de ses principes techniques. Des principes qui n’ont cessés d’être améliorés depuis par les connaissances et les évolutions technologiques mais qui demeurent inchangés dans leurs fondements jusqu’à ce jour.
Les horlogers adoptent le principe de Huygens et prennent vite conscience que l’influence des variations thermiques et de l’équilibre (développement concentrique du spiral) est significative. En 1766, John Harrison imagine un système de compensation thermique. Une lame bimétallique commande les mouvements de la raquette afin de corriger la longueur active du spiral lorsqu’il se dilate ou se contracte. Des horlogers aussi prestigieux que Ferdinand Berthoud, Pierre Le Roy ou A.-L. Breguet affineront les travaux de Harrison ou imagineront leurs propres solutions de compensation thermique (balancier bimétallique, etc.). En 1782, John Arnold, dépose le brevet d’un spiral cylindrique. Celui-ci se développe concentriquement à l’axe du balancier, contrairement au spiral plat de Huygens. Ce type de spiral permet d’obtenir une chronométrie exceptionnelle, particulièrement lorsqu’il est associé à un échappement à détente. La chronométrie, la navigation et donc l’exploration bénéficieront de cette véritable révolution. Le spiral cylindrique exige beaucoup plus d’étapes de fabrication et d’expertise qu’un spiral plat et demande un volume pouvant péjorer significativement l’épaisseur d’un mouvement. C’est pourquoi son usage dans les montres portées se résume à quelques montres d’exception.
Il faut attendre 1919 pour que Charles-Edouard Guillaume, qui a inventé l’Invar vingt-cinq ans auparavant, mette au point l’Elinvar (élastique et invariable). Ce sera l’alliage qui révolutionnera les spiraux par son faible coefficient de dilatation, un module d’élasticité idéal et peu sensible aux champs magnétiques. Il vaudra, avec ses travaux sur l’Invar, à Guillaume le prix Nobel de physique en 1920 et est toujours l’alliage employé dans la fabrication traditionnelle des spiraux.
Depuis 2000, l’application des technologies photo-lithographiques de production de silicium a révolutionné le monde des spiraux. Leur mode de production demande de grandes technologies coûteuses mais son procès est simple à maitriser. Il permet de produire qualitativement à grands volumes. Enfin, le matériau (silicium) présente une excellente élasticité, est non-magnétique et résiste remarquablement à l’usure et la corrosion. Cette méthode de production connait depuis un essor en permanente expansion.
Cette méthode utilise pour matériau, de nos jours encore, l’alliage Elinvar inventé par Ch.-E. Guillaume. Cet alliage complexe à produire est utilisé essentiellement par l’horlogerie et en quantité dérisoire. Une poignée de producteurs le propose à un coût conséquent. Les producteurs d’alliage (fonderies) livrent l’Elinvar en fil d’environ 0,8-1mm de diamètre. Les premières étapes de fabrication d’un spiral consistent à tréfiler ce fil pour en réduire le diamètre. Le fil est tiré dans des filières successives graduellement plus petites. Le diamètre du fil diminue et sa longueur augmente. Aucune matière n’est donc éliminée (usinée) durant ces opérations. Une fois que le diamètre calculé du fil est atteint, on procède à différentes étapes de laminage. Le principe est le même que le tréfilage mais on tire cette fois le fil entre des rouleaux jusqu’à lui donner la section rectangulaire souhaitée. Une fois les dimensions de la section atteintes, on peut couper les lames à leur longueur quasi finale. On donne ensuite la forme du ressort en enroulant plusieurs lames dans des tambours (estrapades) qu’on soumet à différents traitements thermiques extrêmement sensibles à réaliser. Les ressorts se figent ainsi dans leur forme définitive et acquièrent leur propriété élastique. La longueur du ressort est ensuite affinée (coupe intérieure et extérieure), on forme la courbe extérieure et on lui fixe sa virole à l’intérieur et son piton à l’extérieur. On mesure ensuite son module d’élasticité avec un instrument de haute précision sur lequel on mesure également l’inertie des balanciers. Cette étape permet un appairage balancier-spiral idéal pour une chronométrie optimale. Enfin le spiral peut être chassé sur l’axe de son balancier et les nombreuses étapes manuelles, de centrage, mise à plat, équilibrage et réglage peuvent être réalisées. Ses étapes ne peuvent être réalisées qu’à la main et nécessitent une dextérité exceptionnelle.
Marques ou sous-traitants seule une dizaine de maisons maitrise cette méthode de production. De nombreux horlogers et marques sont donc contraints de s’approvisionner auprès d’elles.
Apparu dans l’horlogerie dès l’an 2000, le silicium a littéralement révolutionné la production de nombreux composants et du spiral en particulier. Si la technologie de production est complexe, la production demande beaucoup moins d’expertise et ne nécessite souvent qu’une seule étape automatisée. Cette méthode est celle utilisée pour la fabrication des circuits intégrés. Le principe est de découper (graver) une plaque de silicium d’une épaisseur donnée (généralement celle du composant terminé) par procédé photo-lithographique. Cette méthode permet de réaliser les profils les plus complexes avec une précision atteignant le micron. Selon la taille des composants à réaliser, plusieurs centaines de pièces peuvent être réalisées simultanément sur la même plaque de substrat. Les profils les plus complexes peuvent être obtenus sans l’inconvénient des rayons d’un outil de fraisage ou même du fil d’une machine à électroérosion. Ce procédé n’exerçant aucune contrainte mécanique, il est possible de réaliser des composants très fins (ressorts etc.) ou de les ajourer pour en limiter le poids. Le silicium est un matériau qui présente une dureté supérieure aux aciers, un excellent module d’élasticité et qui est amagnétique. Les progrès de cette technologie et son succès la rendent toujours plus attractive en termes de coûts de production et tends à se généraliser pour la fabrication de nombreux composants (notamment pour l’échappement et l’organe régulateur).