HAIRSPRING STUD HOLDER
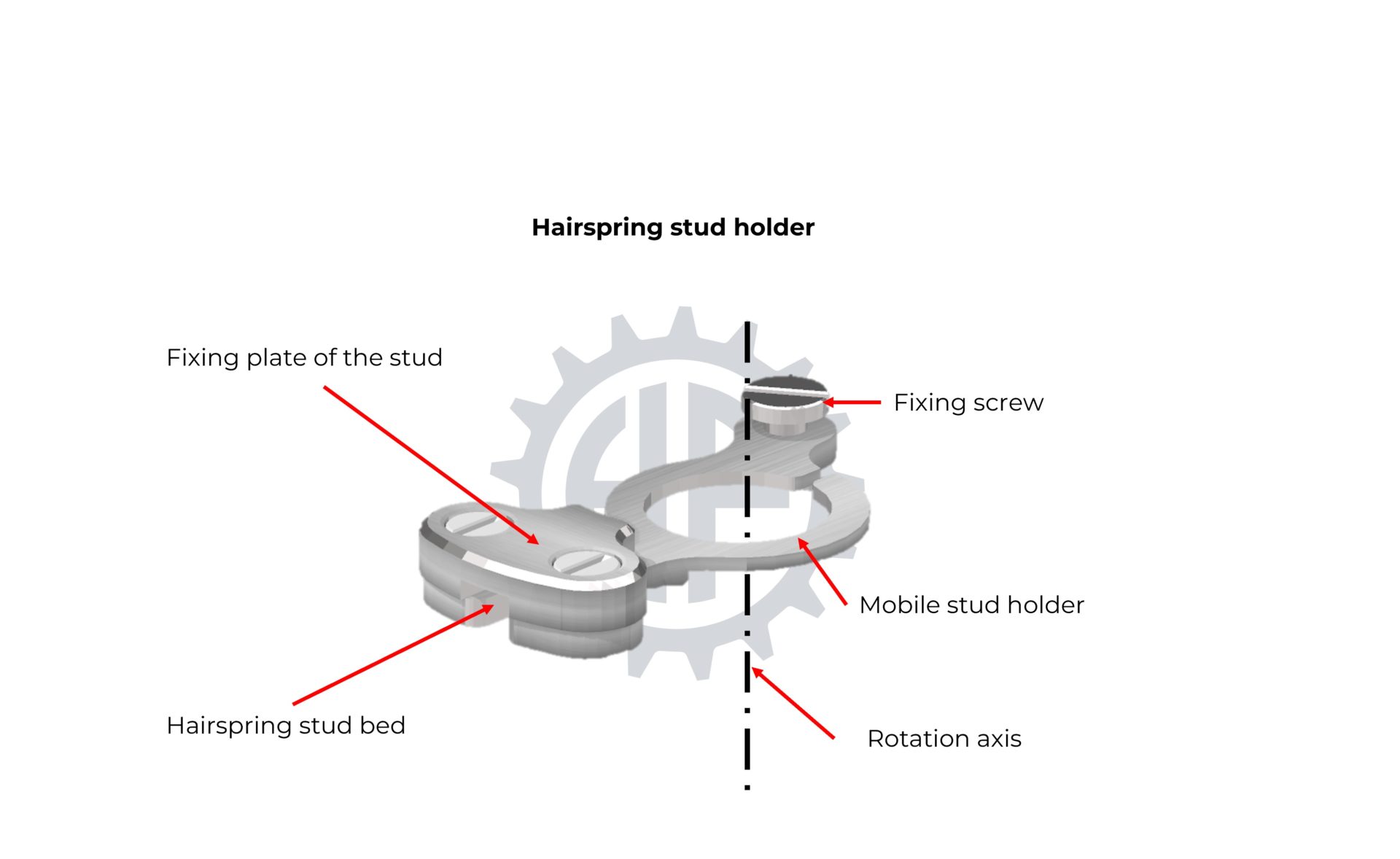
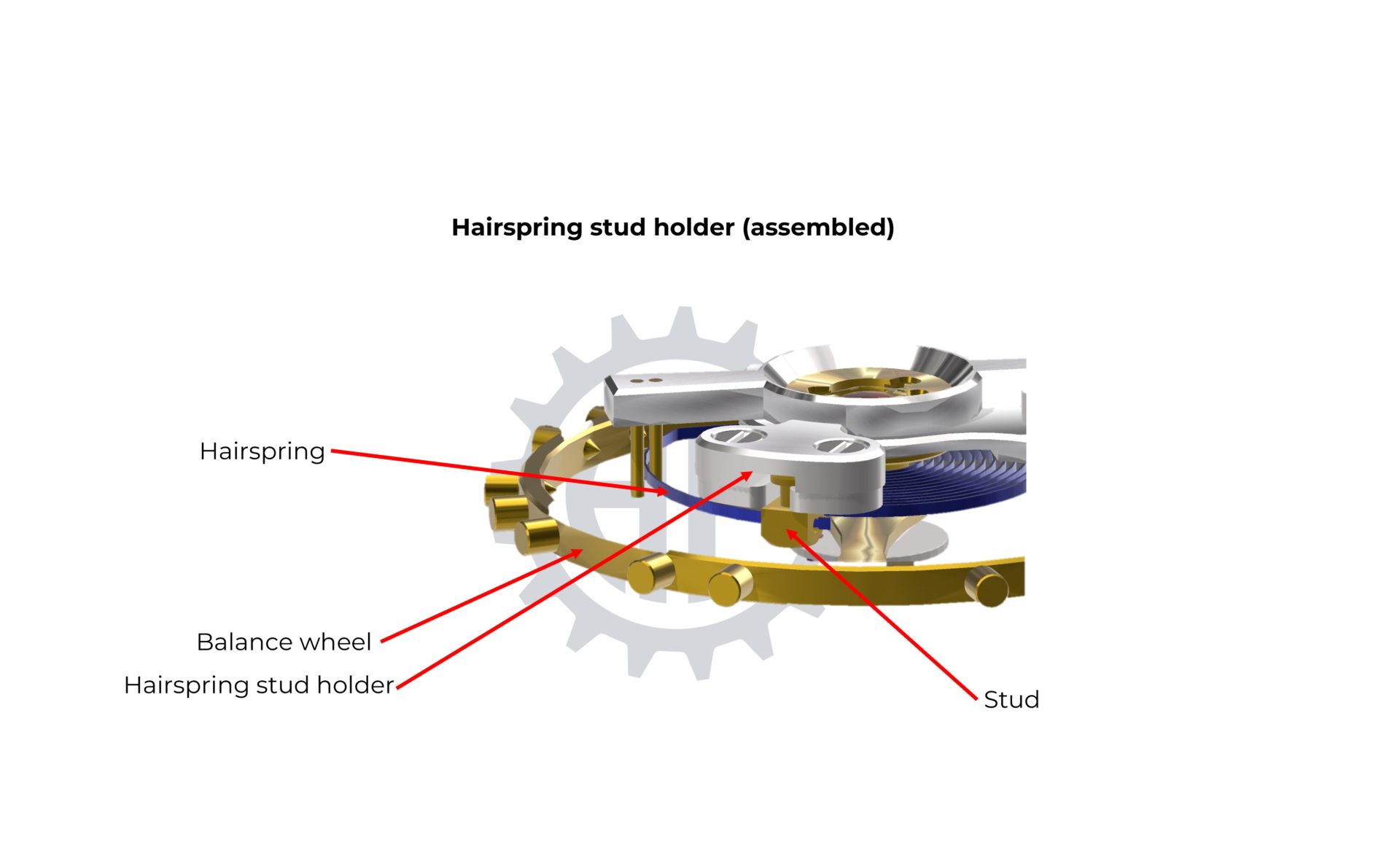
The hairspring stud holder, though not mandatory for all movement constructions and regulation systems, serves to adjust the position of the balance wheel’s rest point, commonly referred to as the reference point. The hairspring stud holder is a mobile component with its axis of rotation at the centre of the balance wheel’s axis. It is secured to the balance cock using the same principle as the index. The hairspring stud, itself attached to the end of the hairspring, fits, and securely fastens to the stud’s holder. By rotating the stud’s holder, the balance wheel is angularly displaced. The reference point is achieved when the watch is unwound (without any energy) and the impulse pin is aligned with the line connecting the escapement wheel, lever, and balance wheel centres. In movements without a hairspring stud holder, the stud is directly fixed to the balance cock in a milled groove in its plate.
The patent for the hairspring stud holder as we know it today is the result of Swiss watchmaker Camille Calame’s work in 1904. However, the earliest mention of the mobile hairspring stud holder dates back to 1889 and is the work of the German watchmaker Richard Lange.
The watchmaker begins the artisanal production of the hairspring stud holder by centring and drilling the centre of its rotation axis on the surface of a steel plate slightly thicker than the finished component. They turn the stud holder’s shoulder using a lathe, centered on the holder’s pivot point. Next, the watchmaker engraves the profile contour of the stud using a tracing tool, focusing on its pivot point. Then, they delicately cut the stud’s contour using a piercing saw. The sides of the piece are then filed to bring the stud to its final thickness and in absolute accordance with its shape. The stud is then angled and polished using custom-made watchmaking tools (files, buff sticks, polishing). According to the rules of the craft, the artisan then stretches the sides of the piece (satin finish). They also calibrate the thickness of the stud to regulate its friction with its staff. This friction must be light enough to precisely modify the stud’s position and strong enough to prevent any inadvertent misadjustment, especially during shocks.
To enhance the cost-effectiveness of manufacturing a single piece or a small series of components, the electrical discharge process proves particularly advantageous. The implementation costs and machine processing time remain relatively low and are suitable for small production volumes. This is followed by a milling operation to remove the countersink from the balance bridge. Compared to the artisanal method, electrical discharge cutting offers a considerable time-saving with good repercussions on the decoration steps. The end of the manufacturing and decoration process is similar to the artisanal method, or the level of finishing required.
Due to the relatively complex shape of the hairspring stud holder, industrial-scale manufacturing favours machining using an automatic lathe capable of performing all machining operations in a single cycle. Finishing and decoration will be done manually or industrially depending on the desired quality. While this method offers the best cost/quality ratio, manufacturing hairspring stud holders using machining centres or stamping is also possible.