L’ANCRE
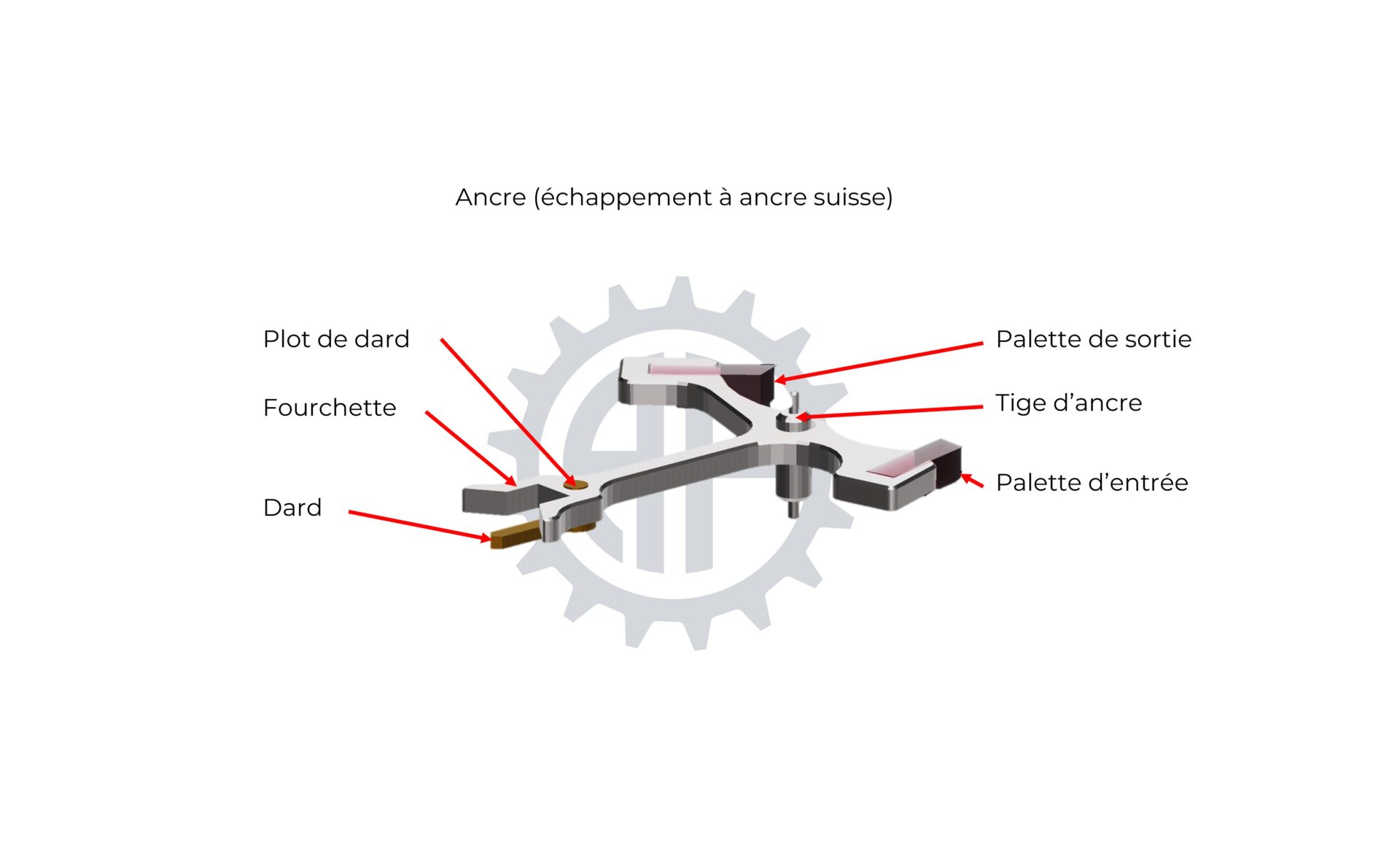
Avec la roue d’échappement et le double plateau, l’ancre est un composant de l’échappement.
La forme de l’ancre et son interaction avec la roue d’échappement et le double plateau (lui-même solidaire de l’axe du balancier) lui permettent de transformer le mouvement rotatif du rouage de finissage en un mouvement oscillatoire. De plus, lorsque le balancier effectue librement son oscillation les palettes de l’ancre bloquent la roue d’échappement et donc l’ensemble du rouage de finissage et le barillet.
L’ancre doit son nom à sa forme et apparait dans différents types d’échappement. L’ancre de l’échappement à ancre suisse, comporte deux palettes en rubis qui bloquent successivement les dents de la roue d’échappement. Lorsque le balancier termine son oscillation libre, la cheville de plateau libère l’ancre qui pivote légèrement. La dent de la roue d’échappement jusqu’alors bloquée transmet, dans un bref mouvement de rotation, son impulsion à l’ancre par le plan d’impulsion de l’ancre qui, par mouvement de bascule est directement transmise au balancier par la fourchette de l’ancre située à l’opposé des palettes.
La planche de l’ancre est généralement en acier ou, de nos jours en silicium. La planche de l’ancre est généralement vissée à la tige d’ancre (son axe). La fourchette est découpée directement dans la planche de l’ancre. A sa base un plot reçoit le dard en laiton qui est chassé au centre de la fourchette au plan inférieur. La fourchette et le dard permettent de transmettre les impulsions reçues de la roue d’échappement au balancier-spiral. Et inversement, d’être dégagée par la cheville de plateau afin de libérer l’énergie du mouvement et de recevoir une nouvelle impulsion. La fourchette travaille avec la cheville de plateau et le grand plateau. Le dard travaille quant à lui avec le petit plateau. Si la fourchette et la cheville de plateau permettent les fonctions de dégagement et d’impulsion, la fourchette dans son interaction avec le grand plateau ainsi que le dard dans son interaction avec le petit plateau permettent de sécuriser l’échappement lors de chocs qui bloqueraient l’ensemble du mécanisme par phénomène de renversement.
L’usage d’une ancre dans différents types d’échappement d’horloges puis de montres date du début du 18ème siècle. Et Thomas Mudge invente l’échappement à ancre suisse en 1754. C’est ce type d’échappement qui est largement le plus utilisé depuis l’aube du 20ème siècle. En soit l’ancre n’as pas connu de grandes évolutions depuis son invention. Jusqu’à la fin du 19ème siècle, les horlogers compensaient fréquemment les défauts d’équilibre de l’ancre dus à sa forme asymétrique en y apposant un contrepoids. L’histoire révélera qu’il est préférable de privilégier la légèreté de l’ancre à son équilibre et les contrepoids ont dès lors été abandonnés. Les autres jalons historiques sont liés aux matériaux utilisés. Ainsi, les palettes de l’ancre, jadis en rubis naturel, sont depuis la moitié du 20ème siècle remplacés par des palettes en corindon synthétiques tout comme l’ensemble des pierres d’une montre. Enfin, l’apparition du silicium au début du 21ème siècle permet de produire des ancres plus légères, plus robustes et amagnétiques.
La méthode la plus artisanale pour fabriquer une ancre consiste à tracer puis découper au bocfil le profil de l’ancre dans une plaque d’acier. Les cotes finales seront atteintes par limage et adoucissement des surfaces. Le plot qui tient le dard sera reporté et fixé à la planche de l’ancre par deux pieds pour un positionnement précis et stable. Le dard cylindrique au niveau du plot est aplati par forgeage limé pour assurer sa fonction. La tige de l’ancre sera tournée puis pivotée. Des machines anciennes et manuelles, ou plus récentes et motorisées permettent de meuler les palettes en rubis afin de leur donner leurs dimensions exactes et de contrôler l’angle des plans d’impulsions. Une fois les composants de l’ancre fabriqués et décorés, l’artisan procède à son assemblage. Le dard est ainsi chassé dans son plot, la planche est généralement vissée sur la tige d’ancre et les palettes maintenues dans leurs pinces par de la gomme laque qui permet, en la chauffant légèrement, d’ajuster la position exacte de chaque palette et d’en assurer fermement la fixation lorsqu’elle est froide.
A l’échelon industriel, la tige de l’ancre sera tournée sur une décolleteuse avant que ses pivots ne soient roulés. L’étampage est particulièrement adapté à la fabrication de la planche, bien que celle-ci puisse également être usinée. Les palettes sont produites sur des machines automatiques dotées de meules en diamant. Selon le niveau de finitions requis on polira les planches d’ancre à la main ou en masse dans des tambours de polissage. Enfin, l’usage de colle pour fixer les palettes supplante aujourd’hui la gomme laque dans la production industrielle.
La méthode hi-tech ne concerne que la planche de l’ancre, ses autres composants étant fabriqués avec les matériaux et la méthode industriels.
La matière (le silicium) et le procédé de fabrication décrit ici sont identiques à ceux utilisés pour la fabrication des circuits intégrés dont ils sont une application. Apparue dans l’horlogerie au tout début du 21ème siècle, cette méthode offre de nombreux avantages.
Le principe est de découper (graver) une plaque de silicium d’une épaisseur donnée (généralement celle du composant terminé) par procédé photo-lithographique. Cette méthode permet de réaliser les profils les plus complexes avec une précision atteignant le micron. Selon la taille des composants à réaliser, plusieurs centaines de pièces peuvent être réalisées simultanément sur la même plaque de substrat. Les profils les plus complexes peuvent être obtenus sans l’inconvénient des rayons d’un outil de fraisage ou même du fil d’une machine à électroérosion. Ce procédé n’exerçant aucune contrainte mécanique, il est possible de réaliser des composants très fins (ressorts etc.) ou de les ajourer pour en limiter le poids ce qui est particulièrement bénéfique s’agissant de l’ancre. Le silicium est un matériau qui présente une dureté supérieure aux aciers, un excellent module d’élasticité et qui est amagnétique. Les progrès de cette technologie et son succès la rendent toujours plus attractive en termes de coûts de production et tend à se généraliser pour la fabrication de nombreux composants (notamment pour l’échappement et l’organe régulateur).