BRIDGES
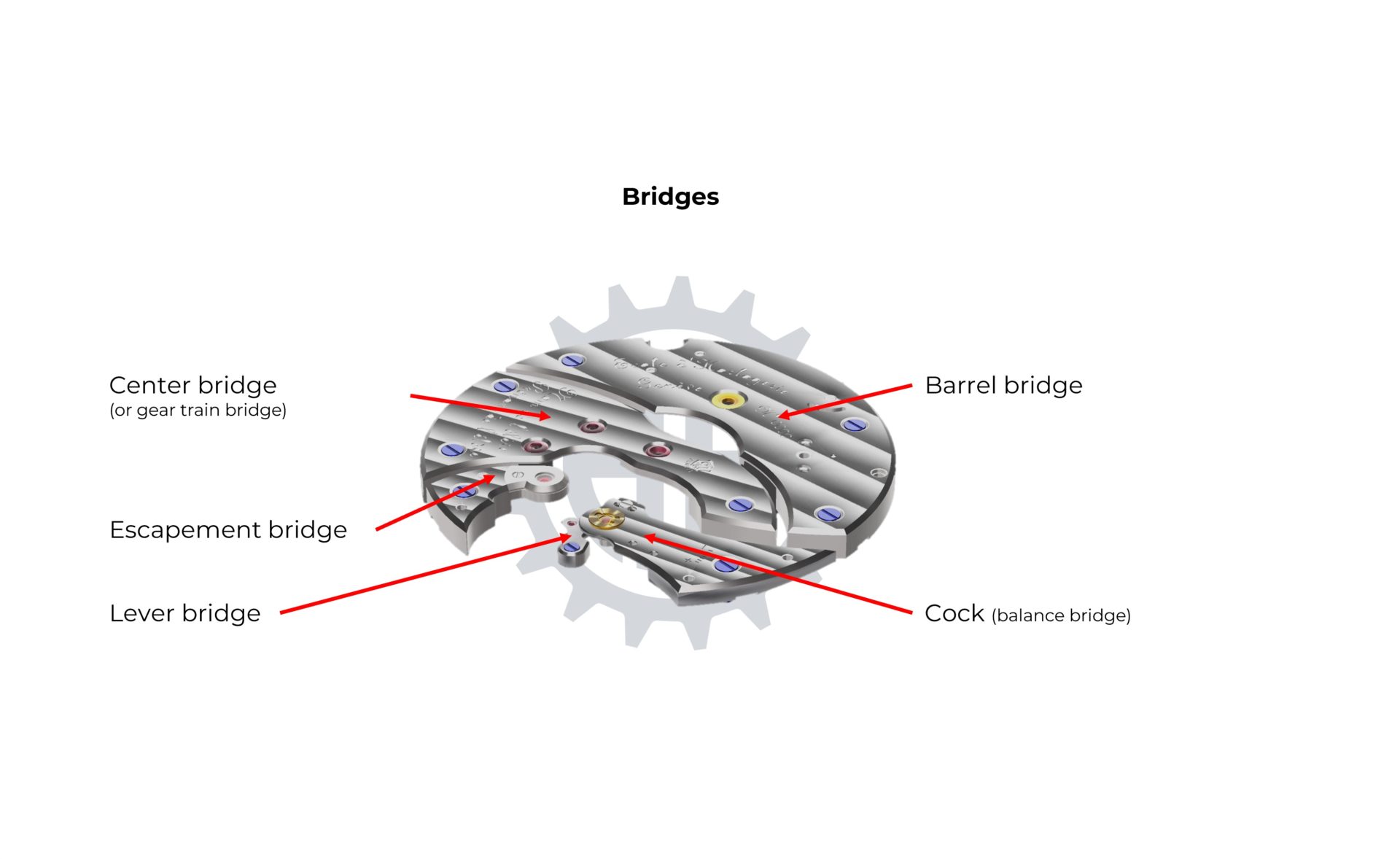
The ensemble of the mainplate and bridges forms the structure of the movement (referred to as the movement cage). It is between the plate and its bridges that the mobile elements of the movement (gears, pinions, lever, balance wheel, etc.) are held. The lower and upper surfaces of the bridges also serve as a fixing support for many fixed components (springs, index-assembly, etc.).
Due to their structural function, the bridges must be perfectly rigid. This constraint requires the use of a variety of materials. Traditionally made of brass, bridges are now frequently manufactured in gold, sapphire, carbon, etc. The design of the bridges, their number, and their arrangement revolve around the centring of the gear-train to create a harmonious structure that enhances the succession of curves in the gear train.
Except for monumental clocks (installed in towers, bell-towers, etc.) where the gears evolve being held by an iron frame (chassis, cage), the components of watches and pendulums always move between a mainplate and bridges or between two mainplates. The most visible bridges of early watches (16th and 17th centuries) were often finely decorated (openwork, engraving, etc.). Between the late 18th and early 19th centuries, the use of bridges dedicated to a component, or a group of components became widespread. Initially rough in manufacturing and with simple geometric shapes, the bridges quickly evolved into aesthetic elements (elaborate shapes) and finely decorated (engraving, gem setting, enamelling, skeletonizing, etc.).
With the era of industrialization, the use of machines became widespread and machining traces became noticeable. Efforts are made to eliminate the latter, which is also achieved through mechanical processes (circular graining, Geneva stripes, etc.). Starting from the second half of the 20th century, new materials were used to fabricate bridges (sapphire, composites, etc.). Thanks to advances in technology, it is now possible to manufacture high-precision ball bearings with very small dimensions. While their efficiency may not match that of construction between mainplate and bridges, they can, in some cases, support a mobile at one end of its axis, like a flying tourbillon cage. This option is favoured for aesthetic reasons or an ultra-thin construction.
There are several methods and different tools that can be used in the artisanal production of bridges.
The first step involves cutting the outline of the bridge shape. According to the artisanal method, this cutting is done with a piercing saw. The sides are then filed to bring them to their final dimension and smooth the surface.
Before machining the hollows of the bridges, the watchmaker must perform an important step that requires absolute precision. For optimal movement performance, the axis of each component must be perfectly positioned relative to the others. Centring is done using a centring machine, which defines the centres of various holes and turnings to be made later. With the centres defined, the watchmaker can proceed to the numerous drillings (axis of mobile components, posts, screw holes, feet, etc.). They will now be perfectly positioned, allowing optimal indexing of the face-lathe for different turning steps.
The face-lathe is the artisan’s tool par excellence. It is a miniature bench lathe that the watchmaker typically fixes in a vice. The watchmaker first manually adjusts the depth of the cut. Then, simultaneously, he starts to operate a chisel that drives the lathe and a second chisel that moves the graver. By combining the rotation speed of the mainplate and the movement speed of the graver, the watchmaker adapts the combination of these two speeds with their sensitivity to achieve precise dimensions and finishes, ensuring both aesthetics and proper functioning.
A bench lathe or a mechanical bench lathe often replaces the face-lathe. The use of such a machine does not compromise the artisanal aspect of the method. It offers a relative timesaving compared to the face-lathe and achieves the same technical and aesthetic quality.
The emergence of CNC machines and their widespread use since the late 20th century have imposed them as the main production tool for bridges and mainplates. While some artisans or prototypists still use artisanal methods, most bridges are produced with CNC machining centres. Generally, these machines can perform all machining operations required for crafting a bridge (milling, drilling, tapping, etc.). Depending on the needs and technical specifications of the bridges, machines may have different capacities (3, 4, 5, and 6 axes). A conventional bridge can usually be perfectly machined on a 3-axis machine. While this machining method, due to the setup and implementation time it requires, favours the profitability of large-scale production, it is also appreciated for small series and even in prototyping for its versatility and “standardization” of use.
According to the range of timepieces, some or all the decoration operations may be performed during machining operations. Today, one can diamond-cut an angle or mill Geneva stripes on the same machine that machined the bridge, during the same work cycle. High-end production often relies on more artisanal decoration methods (trimming, beveling, engraving, etc.).
According to industrial practices, once entirely machined and decorated, the bridge will receive a surface treatment to protect it from oxidation and enhance its aesthetics.
While galvanic treatments (rhodium plating, gilding, etc.) are still widely used, physical vapour deposition treatments (PVD, DLC, etc.) are becoming more prevalent. These treatments have reached an optimal level of quality, being harder and thus less vulnerable to impacts and scratches than a galvanic treatment. They offer an expanding range of colours while perfectly reproducing galvanic shades.
Before accommodating all movement components, the bridge must first be pre-assembled. All the “fittings”, such as jewels, posts, and feet, should be fixed on it. The entirety of these operations (industrially called T-0) can be performed by watchmakers assembling the movement, specialized operators, or even be fully automated.
As with mainplates, hi-tech technologies can be implemented for certain bridge manufacturing steps. Electrical discharge or laser cutting, for example, can be useful for open work, skeletonizing, or decorating. In the case of non-metallic materials (ceramics, plastics, composites, sapphire), injection may precede traditional machining operations. In these cases, machining operations will always require high-tech machines and tools and expertise to meet technical challenges (e.g.: material hardness) and tolerances. Surface treatments (generally subcontracted) are mostly high-tech (PVD, DLC, CVD, ALD, etc.).