LA RAQUETTE
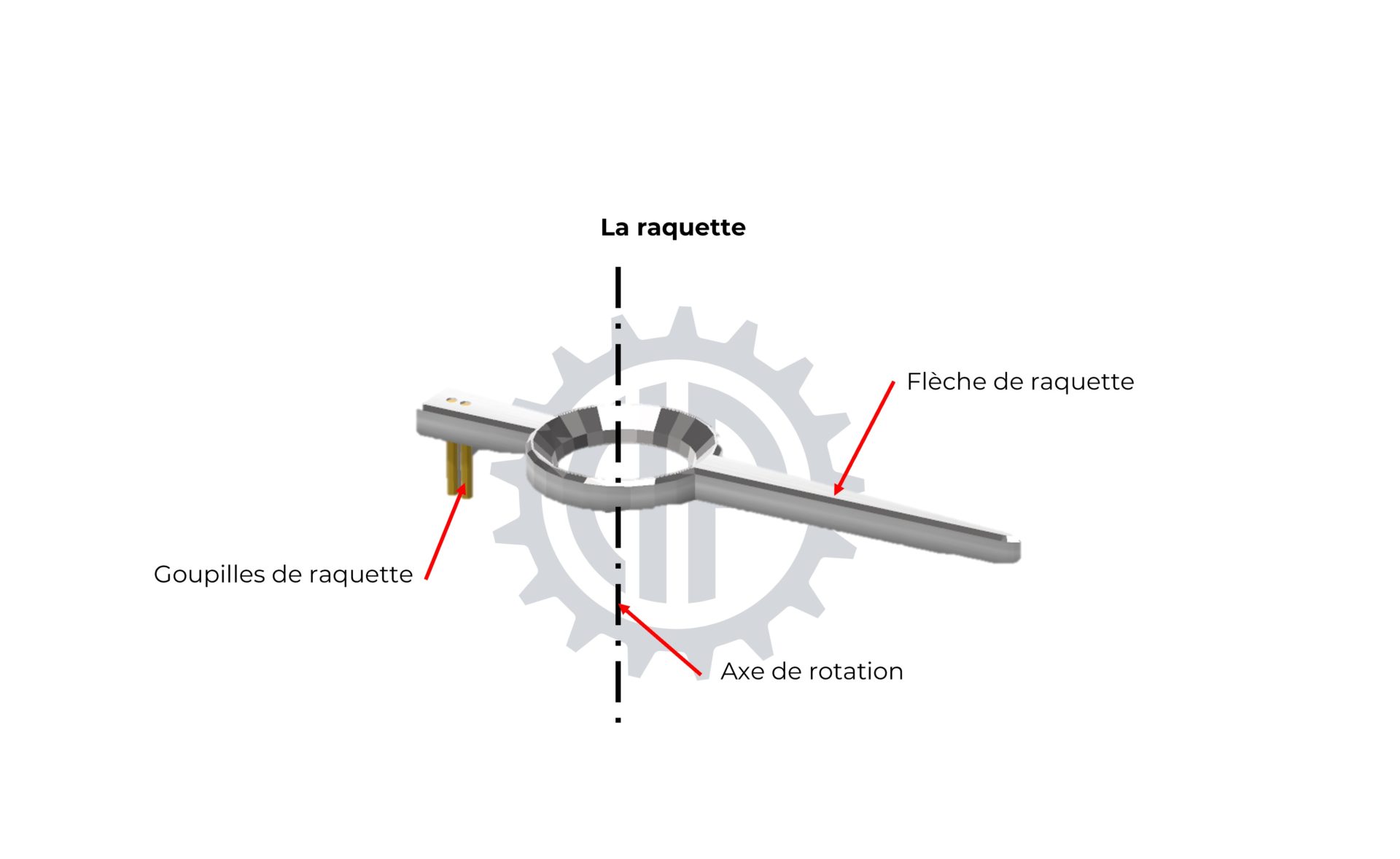
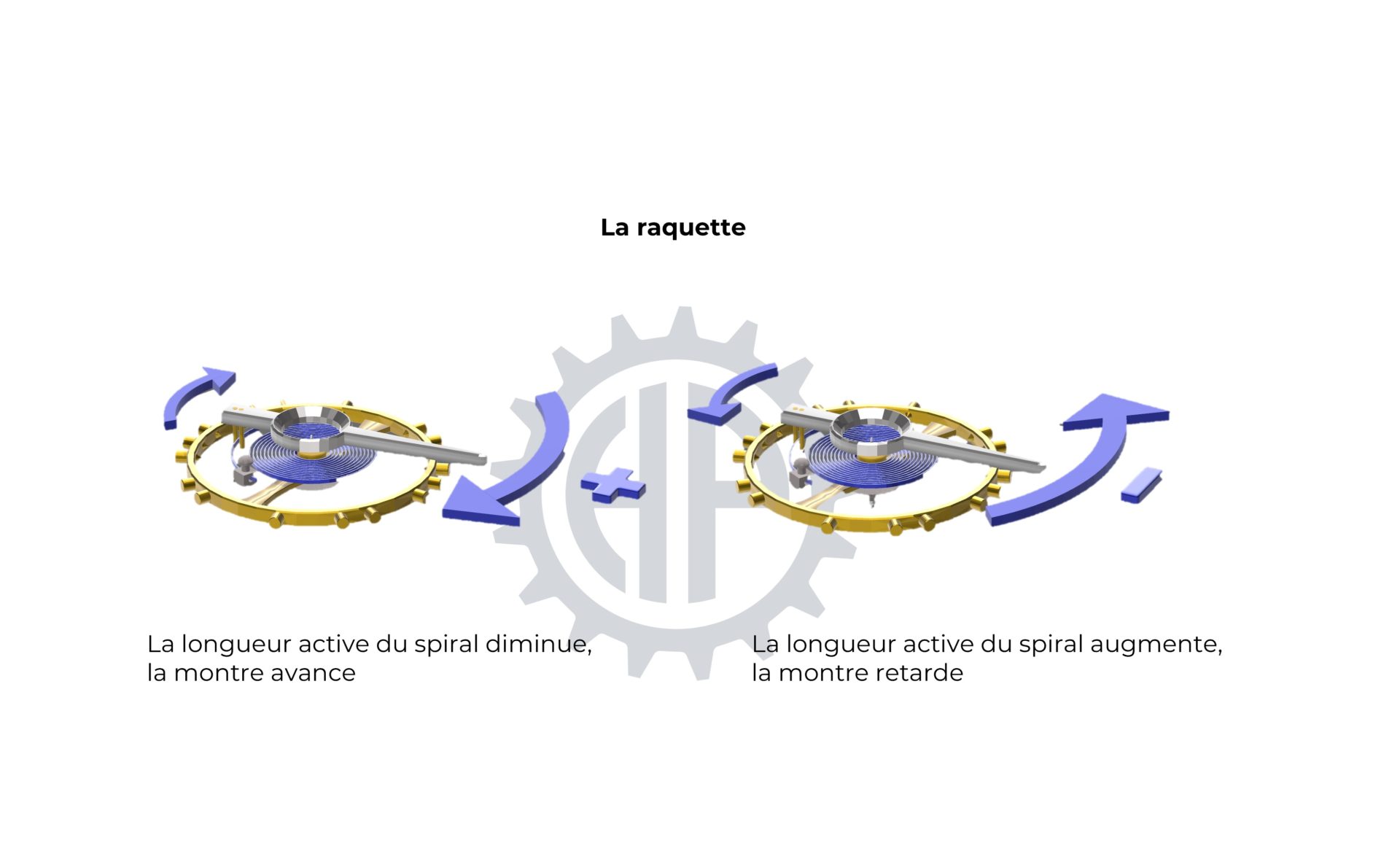
La raquette est généralement en acier. Elle permet de corriger la marche de la montre (avance et retard) en modifiant la longueur active du spiral. Comme souvent en horlogerie, son nom lui vient simplement de sa forme. Son grand cercle lui sert de point de pivotement autour de son noyau. Le tout étant concentrique à l’axe du balancier et positionné sur le dessus du coq (pont de balancier). Son bras le plus long est appelé la flèche de la raquette. Sous son bras le plus court, opposé à la flèche, sont chassées deux goupilles en laiton qui forment la clé de raquette. La spire extérieure du spiral (plat) passe entre les deux goupilles de la clé de raquette et s’appuie sur la goupille intérieure lorsque le spiral est en contraction et sur la goupille extérieure lorsque le spiral est en extension. La position de la clé de raquette définit donc la longueur active du spiral. En déplaçant la flèche de raquette on augmente ou on diminue ainsi la longueur active du spiral, corrigeant, de fait, le réglage de la montre (avance – retard). Les spiraux qui ne sont pas plats (courbes terminales, cylindriques, sphériques etc.) ne permettent l’usage d’une raquette. De plus, les balanciers à inertie variable, toujours plus courants, permettent aujourd’hui de se passer totalement de raquette.
Les premiers composants pouvant être liés à l’ensemble que nous appelons aujourd’hui « raquetterie » apparaissent logiquement avec l’invention du balancier spiral comme régulateur par Christian Huygens en 1675. Pourtant les premières montres ainsi régulées ne comportaient pas vraiment de raquette. Il semblerait que l’apparition de la première raquette soit due à John Harrison sur son célèbre chronomètre H4 en 1759. La raquette imaginée par Harrison n’a pas pour vocation de permettre une correction moyenne du réglage en modifiant statiquement la longueur active su spiral comme c’est le cas de nos jours. Harrison, déjà conscient de l’influence des variations thermiques, conçoit et place la raquette de son H4 pour compenser thermiquement les dilatations et contractions du spiral. Pour y parvenir il capitalise ses travaux sur les constructions bimétalliques (qui lui ont déjà valu l’invention du balancier bimétallique thermo-compensateur. La raquette s’articule sur une double lame composée de deux métaux différents. Par leur combinaison, la raquette s’inclinera à gauche lorsque les températures descendent et à droite lorsqu’elles montent. Les mouvements de la raquette étant opposés à ceux du spiral (dilatation-contraction), la raquette corrige la longueur active du spiral lors des variations de températures. Très complexe à maitriser, ce système ne connaitra pas un grand essor et perdra rapidement de son intérêt lorsque la maitrise des matériaux, et des théories de réglages progresseront. La raquette est cependant présente dans la majeure partie des montres depuis et jusqu’à nos jours, mais dans son rôle d’ajustement statique du réglage de la montre (correction de la longueur active du spiral)
L’horloger commence la fabrication artisanale de la raquette en pointant et perçant le centre de son axe de rotation à la surface d’une plaque d’acier d’une épaisseur légèrement supérieure à celle du composant terminé. Il grave ensuite le contour du profil de la raquette à l’aide d’une pointe à tracer en se centrant sur le point de pivotement. Puis il découpe délicatement le contour de la raquette à l’aide d’un bocfil. Les flancs de la pièce sont ensuite limés pour amener la raquette à son épaisseur finale et dans le respect absolu de sa forme. La raquette est ensuite anglée et polie à l’aide des outils usuels (limes, cabrons, polissage). Une grande moulure est généralement polie en son centre. Selon les règles de l’art, l’artisan étire ensuite les traits des flancs de la pièce (satinage) et de l’infime plat qui reste sur la surface supérieure de la raquette. De ce fait, il calibre également l’épaisseur de la raquette afin de réguler sa friction avec le noyau de raquette. Cette friction doit être suffisamment légère pour permettre de modifier précisément la position de la raquette et suffisamment forte pour éviter tout déréglage intempestif, lors de chocs notamment.
Pour optimiser les coûts de production d’une pièce unique ou d’une petite série de composants, l’électroérosion est ici particulièrement intéressante. Les coûts de mise en œuvre et le temps de passage en machine demeurent relativement faibles et adaptés aux petits volumes de production. De plus, cette technologie permet de découper des profils complexes et fins sans exercer la moindre contrainte mécanique sur le composant lors de sa fabrication. En rapport à la méthode artisanale, la découpe par électroérosion offre un gain de temps considérable avec de bonnes répercussions sur les étapes de décoration. La fin du processus de fabrication et de décoration s’apparente à la méthode artisanale ou au niveau de finitions requis.
Une production en grande(s) série(s) justifie l’investissement d’une étampe (outil de frappe) pour fabriquer des raquettes à un coût optimal. Le contour élargi du profil est ainsi poinçonné directement dans une bande d’acier d’une épaisseur légèrement supérieure à celle du composant terminé par une presse à étamper. Des étapes manuelles demeurent toutefois incontournables. On doit ainsi amener la raquette à ses cotes finales (profil et épaisseur) tout en lui apportant les finitions et les décorations souhaitées (satinage, anglage, polissage etc.).