CANNON-PINION
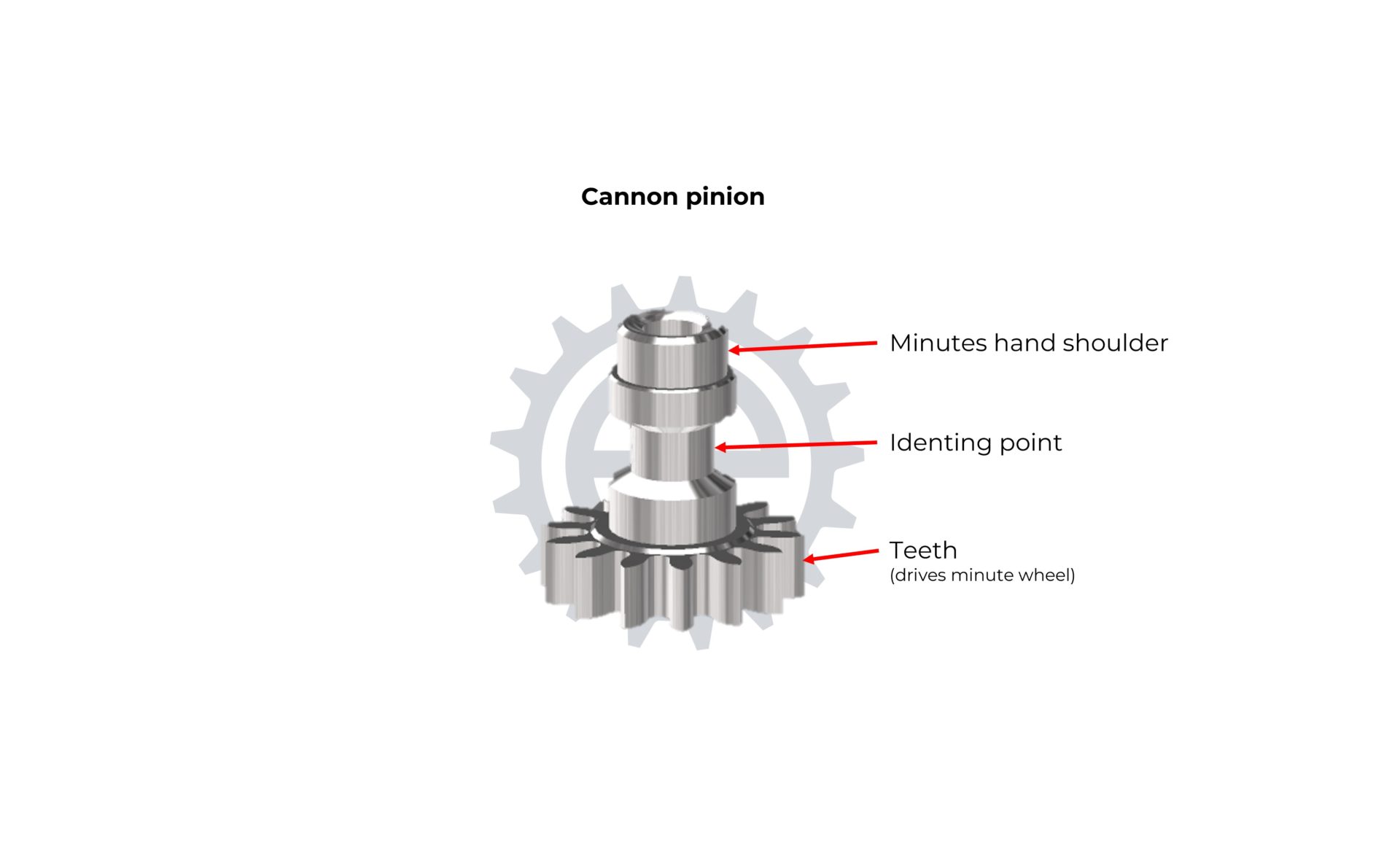
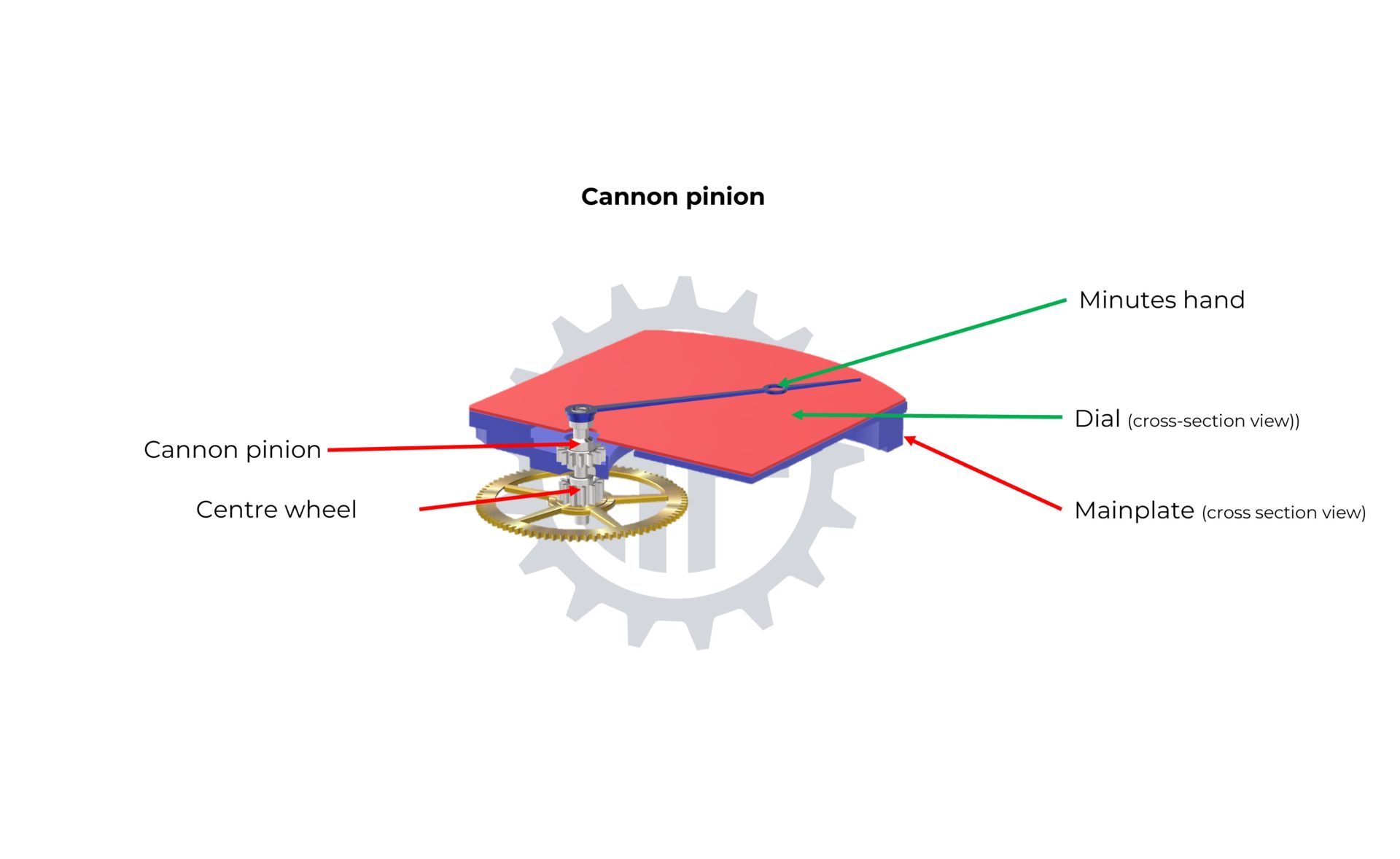
The cannon pinion passes through the mainplate and emerges, usually at the centre of the movement, on the dial side of the watch. It is a cylindrical tube, typically blind when there are no central seconds hands, at the base of which teeth are cut into a larger diameter. The cannon is fitted onto the pivot-shank, previously lubricated. To enable the cannon to be driven by the centre-pinion, a groove (undercut) is made on the pivot shank of the centre-pinion. The tube of the cannon is then pinched at the same level as the undercut on the pivot-shank. This pinching creates sufficient grip for the cannon to be driven by the centre-pinion. Additionally, it is light enough to allow the cannon to turn freely on the centre-pinion during the watch-setting process. This friction is known as “indenting.” A good indenting is considered adequately greased when the movement can be stopped during anti-clockwise time-setting.
Once driven by the centre-pinion, the cannon pinion rotates at the same speed (1t/h) and can directly carry the minute hand, which is set on its top surface. The teeth of the cannon pinion drive the minute wheel, whose pinion subsequently can drive the hour wheel stacked on top of the cannon pinion.
Cannon pinion is a relatively simple component, regardless of the method used. It is a cylindrical steel pinion without pivots. All the necessary operations for its manufacture can be carried out using a lathe and a universal dividing head (turning, tooth cutting). The cannon pinion is entirely polished to minimise friction, especially on surfaces in contact with the hour wheel. This step is also achievable on a conventional lathe. Finally, and in most cases, the artisan will carry out any heat treatments required by the chosen steel alloy (quenching, tempering, annealing). The watchmaker then whitens all surfaces of the cannon pinion, which may have been discoloured by the successive heat treatments.
On an industrial scale, the cannon pinion can be entirely manufactured by an automatic lathe. Its production is straightforward, involving a few turning operations and tooth cutting. The cannon pinion is entirely polished to minimise friction, especially on surfaces in contact with the hour wheel. Depending on the alloy chosen for its production, the cannon pinion will then undergo heat treatments to achieve optimal hardness.