WINDING STEM
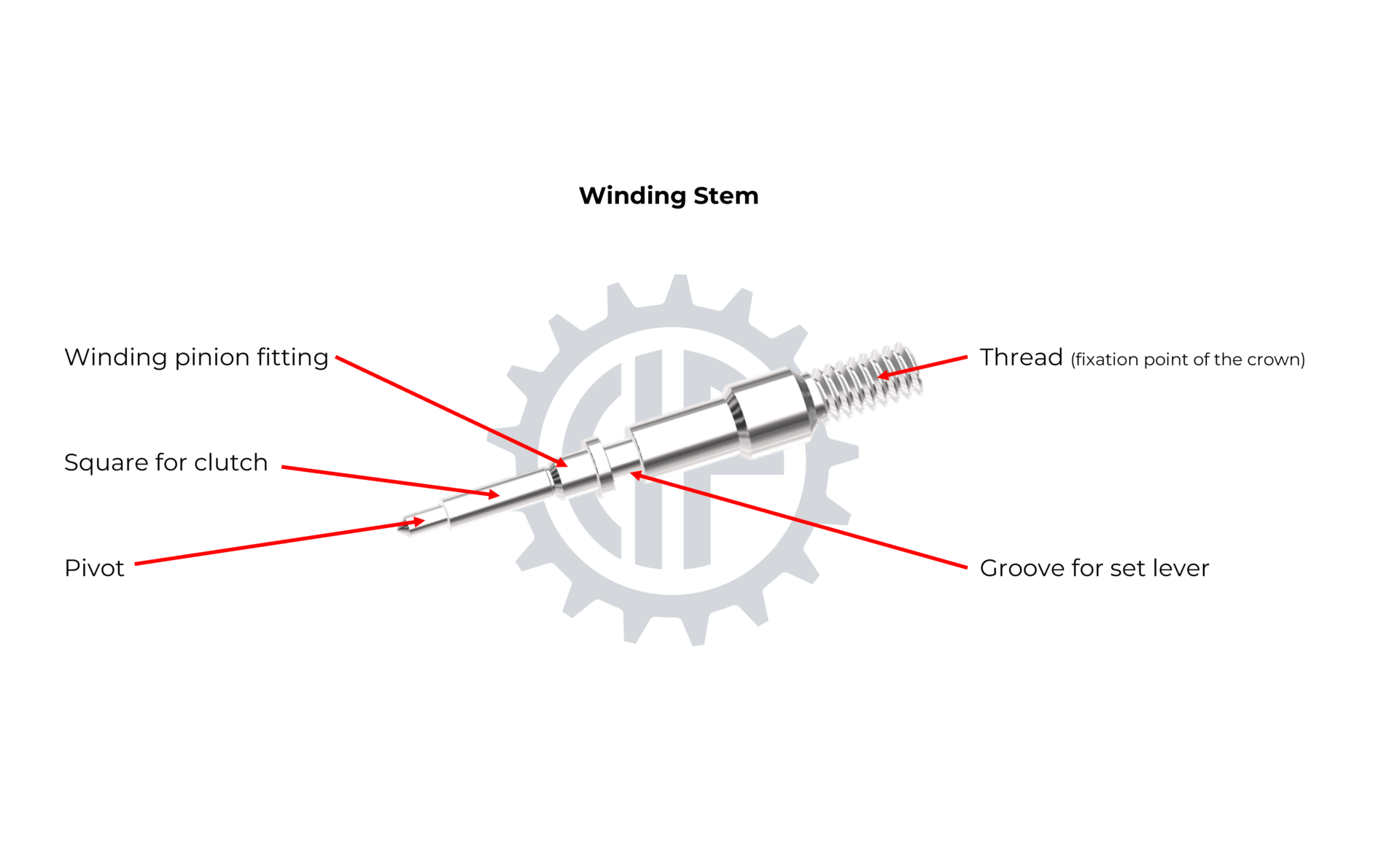
The winding stem serves as a control element, facilitating corrections and connecting the internal and external components of the watch case. Crafted from steel, it is linked to the movement through a blind hole perpendicular to the hands‘ axis. At its inner end, the winding stem features a pivot, allowing it to rotate freely around its own axis. Following the pivot is a long square on which the sliding pinion moves. The movement of this pinion is crucial for engaging the winding mechanism (pushed stem) and the time-setting mechanism (pulled stem). After the square of the sliding pinion, a cylindrical fitting accommodates the winding pinion. This pinion rotates freely on the stem and will only be driven when the sliding pinion engages it through their common Breguet tooting. A groove on the diameter of the winding stem, closest to the periphery of the mainplate, receives the setting lever stud, fixing the stem to the movement and allowing the operation of the setting lever.
The setting lever is a lever that activates the yoke, which, in turn, makes the sliding pinion slide on the square of the winding stem, alternating between functions (time-setting, winding). In its external part outside the movement, the winding stem is entirely threaded. It passes through the case tube, and after careful adjustment of the winding stem’s length, it receives the crown that screws directly onto it and ensures that the watch is water-resistant both inside and outside the case tube.
Typically, on a simple watch, when the crown (and thus the winding stem) is pushed (against the case), the crown and the winding stem control the winding mechanism. When the crown and the stem are pulled, they control the time-setting mechanism. An intermediate position usually allows for adjusting a date when the watch displays one. Other corrections may be assigned to the crown (multiple time zones, perpetual calendar, etc.). In these cases, and to multiply the possible commands or corrections, it is not uncommon to assign an indicator to be regulated by the direction of rotation of the crown and thus the winding stem.
The winding stem appears with Jean Adrien Philippe’s invention of the winding mechanism in 1842. At this point in history, Antoine Le Coultre had not yet invented the time-setting mechanism, and the stem exclusively operated the winding mechanism, from which the name “winding stem” came in this short period of time. It was only in 1847, five years after Adrien Philippe’s discovery when Antoine Le Coultre invented the setting lever mechanism, which provides the dual winding-time setting function without requiring the use of a key. Since the end of the 19th century, the mechanism has evolved, and depending on the requirements, it has become more complex (date adjustment, other functions). Materials and manufacturing methods have sometimes appeared since the late 20th century, although most constructions remain very traditional in the materials used as well as in the manufacturing methods.
The winding stem is a relatively easy component to manufacture, regardless of the method used. The artisan begins by performing all the turning operations that constitute the bulk of the work, ensuring the turnings’ concentricity given the winding stem’s delicate length-diameter ratio. The artisan can then thread the end of the winding stem on the same lathe. The next step takes place at the workbench, where the artisan files the four faces of the square on which the sliding pinion will slide. This operation requires a certain dexterity as the square is long and must be perfectly regular. The surfaces are then polished or smoothed according to their function, and the winding stem can undergo its heat treatments (quenching and tempering). The thermal treatments of the winding stem are relatively challenging to succeed due to its significant length and small diameter. Thus, the heat treatment may not be homogeneous, and stem deformations are unfortunately always possible during these steps. A brief step of polishing and smoothing will restore the winding stem’s colour, and it will be ready for assembly. Finally, the length adjustment of the stem will be done during the movement’s casing.
Automatic lathe is the most suitable machine for producing winding stems on the industrial level. All operations (turning, threading, and square milling) can be performed in a single cycle. Depending on the chosen steel alloy, the winding stem may not require additional heat treatments. Finally, and depending on the desired level of finishing, the end treatments, particularly polishing, can be done by hand or, on a large scale, in a polishing drum, for example.