LE RESSORT DE TIRETTE
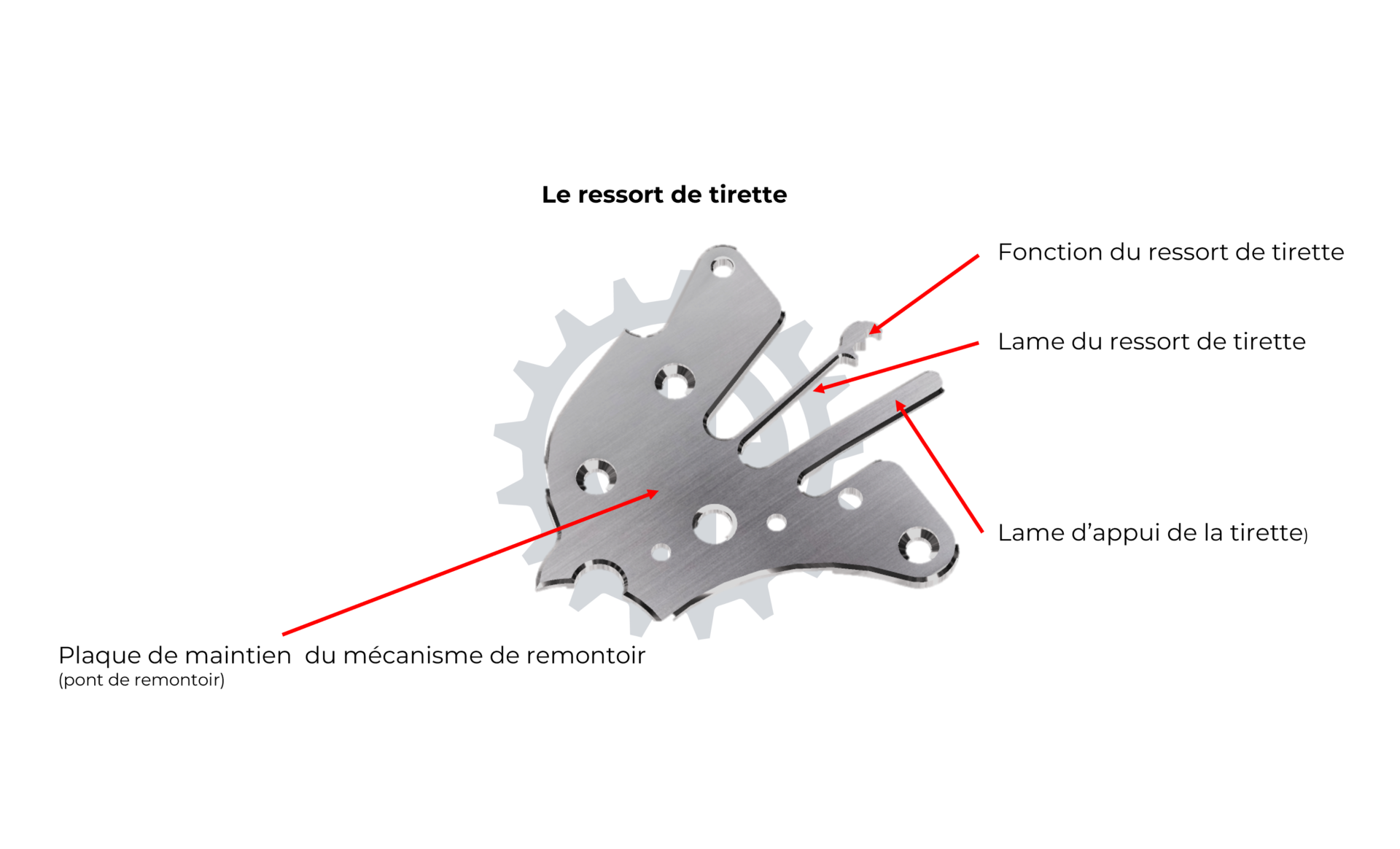
Le ressort de tirette appartient aux mécanismes de remontoir et de mise à l’heure. Il permet de définir les deux positions (remontoir et mise à l’heure) de la tirette et donc, de définir les deux mêmes positions de la bascule et sa course. Dans bien des cas, le ressort de tirette est découpé dans la plaque de maintien (pont) du mécanisme de remontoir.
La tirette, et donc son ressort apparaissent en 1847 avec l’invention du remontoir à bascule d’Antoine Le Coultre dont la bascule est l’élément central. Actionnée par la tirette, la bascule permet de commuter la commande de la couronne entre le mécanisme de remontoir et le mécanisme de mise à l’heure, ad minima.
Les majeures évolutions qui ont été portées à l’invention de Le Coultre ont consistés à multiplier les fonctions ajustables par la couronne.
L’horloger commence la fabrication artisanale du ressort de tirette en gravant son profil à l’aide d’une pointe à tracer sur la surface d’une plaque d’acier d’une épaisseur légèrement supérieure à celle du composant terminé. Il en pointe ensuite les différents perçages (vis et pieds). Puis il découpe délicatement le contour du ressort à l’aide d’un bocfil. Les flancs du ressort sont ensuite limés pour amener le ressort à son épaisseur finale et dans le respect absolu de sa forme. Le talon et la lame du ressort sont ensuite anglés et poli à l’aide des outils usuels (limes, cabrons, polissage). Ces opérations sont particulièrement délicates en raison du profil parfois complexe du ressort de tirette (lorsqu’il compose également le pont de remontoir en particulier). Selon les règles de l’art, l’artisan étire ensuite les traits des flancs de la pièce (satinage) et de l’infime plat qui reste sur la surface supérieure du ressort.
Les traitements thermiques et les opérations de blanchissage qui les suivent sont également particulièrement délicats en raison du profil complexe du ressort.
Pour optimiser les coûts de production d’une pièce unique ou d’une petite série de composants, l’électroérosion est ici particulièrement intéressante. Les coûts de mise en œuvre et le temps de passage en machine demeurent relativement faible et adaptés aux petits volumes de production. De plus, cette technologie permet de découper des profils complexes et fins sans exercer la moindre contrainte mécanique sur le composant lors de sa fabrication. En rapport à la méthode artisanale, la découpe par électroérosion offre un gain de temps considérable avec de bonnes répercussions sur les étapes de décorations. La fin du processus de fabrication et de décoration s’apparente à la méthode artisanale ou au niveau de finitions requis.
Une production en grande(s) série(s) justifie l’investissement d’une étampe (outil de frappe) pour fabriquer des ressorts de tirette à un coût optimal particulièrement quand le ressort de tirette tient également le rôle de pont de mécanisme de remontoir et présente dès lors un profil complexe. Le contour élargi du profil est ainsi poinçonné directement dans une bande d’acier d’une épaisseur légèrement supérieure à celle du composant terminé par une presse à étamper. Des étapes manuelles demeurent toutefois incontournables. On doit ainsi amener e ressort de tirette à ses cotes finales (profil et épaisseur) tout en lui apportant les finitions et les décorations souhaitées (satinage, anglage etc.).