LES PONTS
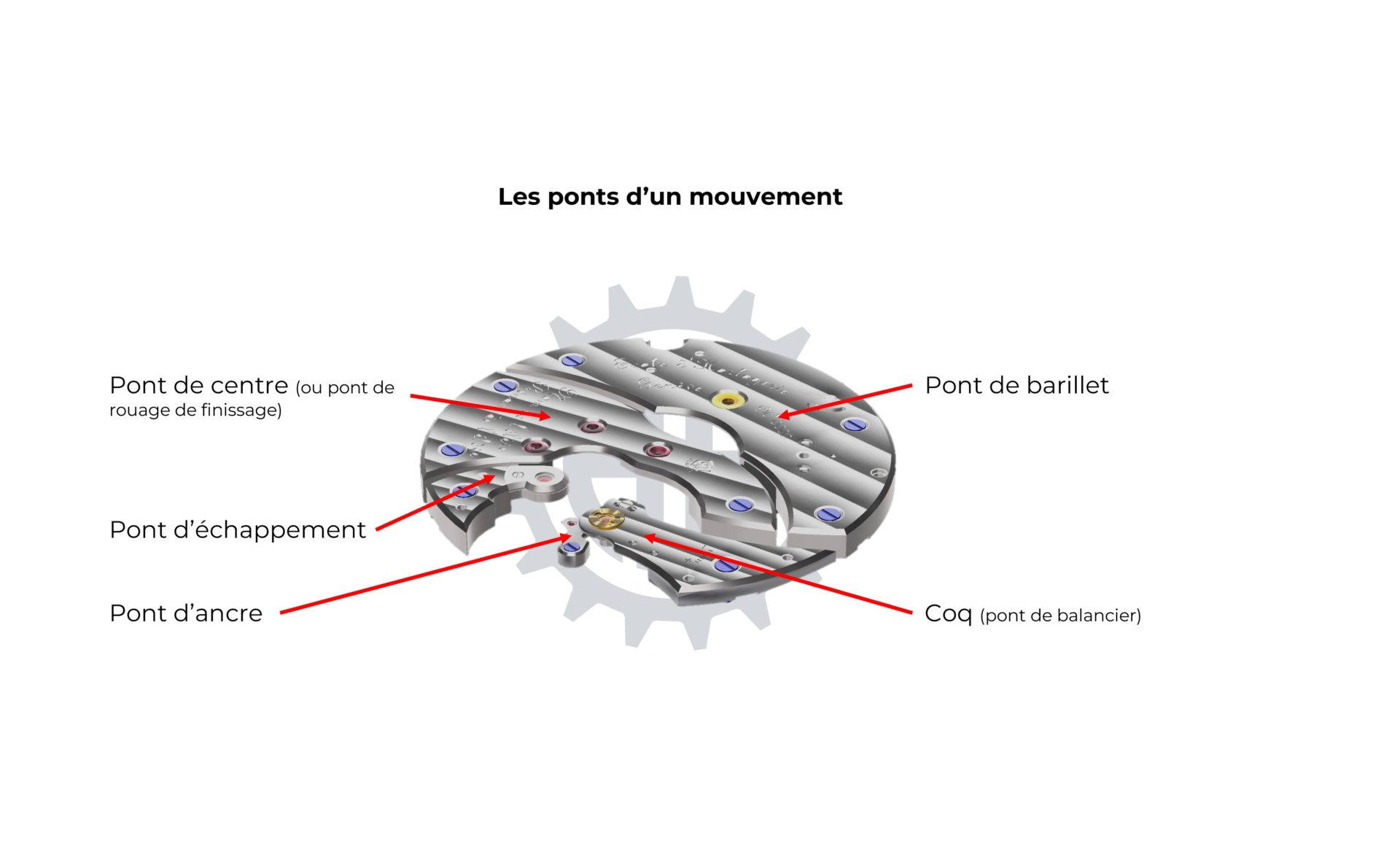
Avec la platine, l’ensemble des ponts constitue la structure du mouvement (on parle de la cage de mouvement). C’est entre la platine et ses ponts que sont maintenus les éléments mobiles du mouvement (mobiles, pignons, ancre, balancier etc.). Les surfaces inférieures et supérieures des ponts servent également de support de fixation à de nombreux composants fixes (ressorts, raquetterie etc.).
Par leur fonction structurelle, les ponts doivent être parfaitement rigides. Cette contrainte appelle l’usage d’un grand nombre de matériaux. Traditionnellement en laiton, les ponts sont aujourd’hui fréquemment fabriqués en or, en saphir, en carbone, etc. Le design des ponts, leur nombre et leur disposition sont articulés autour de la position des pointages du rouage afin de représenter une structure harmonieuse valorisant la succession d’arrondis du rouage.
À l’exception des horloges monumentales (tours, clochers etc.) dont les rouages évoluent en étant maintenus par un bâti en fer (châssis, cage), les mobiles des montres et des pendules évoluent toujours entre une platine et des ponts ou entre deux platines. Les ponts les plus visibles des premières montres (16e et 17e siècle) étaient déjà souvent finement décorés (ajourage, gravure, etc.). Entre la fin du 18e et le début du 19e siècle, l’usage de ponts dédiés à un composant ou à un groupe de composants se généralise. D’abord bruts de fabrication et de formes géométriques simples, les ponts deviennent rapidement des éléments esthétiques (formes travaillées) finement décorés (gravure, sertissage, émaillage, squelettage, etc.).
Avec l’ère de l’industrialisation, les surfaces usinées trahissent l’usage des machines. On recherche à éliminer les traces d’usinage et l’on y parvient par des procédés issus eux-aussi de l’industrialisation (perlage, côtes de Genève, etc.). Dès la seconde moitié du 20e siècle, de nouveaux matériaux sont parfois utilisés pour la fabrication des ponts (saphir, composites, etc.). Les progrès de la technologie permettent aujourd’hui de fabriquer des roulements à bille de grande précision et de dimensions très réduites. Si leur rendement n’est pas aussi bon qu’une construction entre platine et ponts, ils peuvent, dans certain cas, permettre de maintenir un mobile par une seule des extrémités de son axe à la façon d’une cage de tourbillon volant. Cette possibilité sera privilégiée pour des raisons esthétiques ou pour une construction ultra-plate.
Plusieurs méthodes et différents outils peuvent s’apparenter à la méthode artisanale.
La première étape consiste à découper le contour de la forme du pont. Selon la méthode artisanale, cette découpe se fera à l’aide d’un bocfil. Les flancs seront ensuite limés pour les amener à leur cote finale et en adoucir la surface.
Avant de procéder à l’usinage des creusures des ponts, l’horloger doit procéder à une étape fondamentale qui requiert une précision absolue. Pour un rendement optimal du mouvement l’axe de chaque composant doit être parfaitement positionné par rapport aux autres. Le pointage est réalisé à l’aide d’une machine à pointer. Il définira les centres des différents perçages et tournages qui seront réalisés ultérieurement.
Les centres étant pointés, l’horloger peut ensuite procéder aux différents et nombreux perçages (axe des mobiles, des tenons, trous de vis, de pieds etc.). Ceux-ci seront désormais parfaitement positionnés et permettront une indexation optimale du burin-fixe pour les différentes étapes de tournage.
Le burin-fixe est l’outil de l’artisan par excellence. Il s’agit d’un tour miniature d’établi que l’horloger fixe généralement dans un étau. L’horloger règle d’abord manuellement la profondeur de la coupe (passe). Il actionne ensuite simultanément une manivelle qui entraine le tour et une seconde qui déplace le burin (outil de coupe). En combinant la vitesse de rotation du pont et la vitesse de déplacement du burin, l’horloger adapte la combinaison de ces deux vitesses par sa sensibilité afin d’obtenir un résultat précis en termes de dimensions ainsi que des finitions garantes d’esthétique et de bon fonctionnement.
Un tour d’établi ou un tour sur banc (motorisés) remplace souvent le burin fixe. L’usage d’une telle machine ne remet pas en cause le caractère artisanal de la méthode. Il offre un relatif gain de temps par rapport au burin fixe et permet d’atteindre la même qualité technique et esthétique que le burin fixe.
L’apparition des machines à commandes numériques et leur généralisation dès la fin du 20e siècle les ont imposées comme principal outil de production des ponts et des platines, parmi d’autres. Si quelques artisans ou prototypistes mettent encore une méthode artisanale en œuvre, la très grande majorité des ponts est produite sur des centres d’usinages à commandes numériques. Généralement, ces machines permettent d’effectuer la totalité des opérations d’usinage que requiert un pont (fraisage, perçage, taraudage, etc.). Selon les besoins, les spécificités techniques des ponts à usiner, les machines pourront être de différentes capacités (3, 4, 5, 6 axes). Un pont « conventionnel » peut généralement être usiné sur une machine évoluant sur 3 axes. Ce mode d’usinage, par les temps de réglage, de mise en œuvre qu’il demande, favorise la rentabilité des productions de grandes séries. On l’apprécie également pour de petites séries et dans la prototypie pour la polyvalence et la « standardisation » de son usage.
Selon la gamme de la montre, une partie ou la totalité des opérations de décoration pourront être réalisées durant l’usinage. On peut aujourd’hui diamanter un angle ou fraiser des côtes de Genève sur la même machine que celle qui aura usiné le pont et durant le même cycle de travail. La production de haut de gamme aura souvent recourt à des méthodes de décoration plus artisanales (ébavurage, anglage, gravure etc.).
Selon les usages industriels, le pont une fois totalement usiné et décoré recevra un traitement de surface pour se protéger de l’oxydation et parfaire son esthétique.
Si les traitements galvaniques (rhodiage, dorage, etc.) restent répandu, les traitements par dépôt en phase vapeur (PVD, DLC, etc.) s’imposent de plus en plus. Ces derniers ont atteint un niveau de qualité optimal, ils sont plus durs et donc moins vulnérables aux chocs et rayures qu’un traitement galvanique et offrent une palette de couleurs qui ne cesse de s’étoffer tout en pouvant reproduire les couleurs galvaniques.
Avant de pouvoir accueillir l’ensemble des composants du mouvement, le pont doit d’abord être pré-assemblé. L’ensemble des « garnitures » du pont telles que les pierres, les tenons, les pieds y sera fixé. L’ensemble de ces opérations (industriellement appelé T0) peut être réalisé par les horlogers qui procéderont à l’assemblage du mouvement, des opérateurs spécialisés voire être totalement automatisé.
Comme pour les platines, des technologies Hi-tech peuvent être mises en œuvre pour certaines étapes de fabrication de ponts. L’électroérosion, la découpe laser pourront par exemple être utiles à des opérations d’ajourage, de squelettage voire de décoration. Dans le cas d’emploi de matériaux non métalliques (céramiques, plastiques, composites, saphir), l’injection précédera parfois les opérations plus traditionnelles d’usinage. Dans ces cas, les opérations d’usinage exigeront des machines et des outils de haute technologie et un savoir-faire à la hauteur des défis techniques (p. ex. : dureté des matériaux) et des tolérances. Les traitements de surface (généralement sous-traités) sont abondamment issus de hautes technologies (PVD, DLC, CVD etc.).